Starched agent and glass powder for forming dielectric for plasma display board
A plasma display panel and glass powder technology, applied in the direction of dielectric/insulating layer, discharge tube/lamp manufacturing, quartz/glass/glass enamel, etc., can solve the problem of large bubble diameter, difficulty in forming a smooth and uniform film thickness, Problems such as poor reproducibility
- Summary
- Abstract
- Description
- Claims
- Application Information
AI Technical Summary
Problems solved by technology
Method used
Examples
Embodiment Construction
[0011] Hereinafter, a paste for forming a dielectric body according to an embodiment of the present invention will be described.
[0012] This dielectric-forming paste is suitable for forming a dielectric layer with a film thickness of 30 to 40 μm on scanning electrodes for plasma discharge formed on a front glass plate of a plasma display panel, and contains glass powder as a main component. The maximum particle diameter D of the glass powder MAX 15μm or less, 90% particle diameter D 90 7μm or less, 75% particle diameter D 75 4μm or less, 50% particle diameter D 50 3μm or less, 25% particle diameter D 25 Below 2μm, the specific area is 1.0~4.0m 2 / g. When the particle size distribution of the glass powder is limited in this way, the gaps between the glass powder particles are very small, so there are very few bubbles in the fired dielectric layer, and the remaining bubbles are also very small, and the light transmittance is 76%. above. In addition, the surface smoothne...
PUM
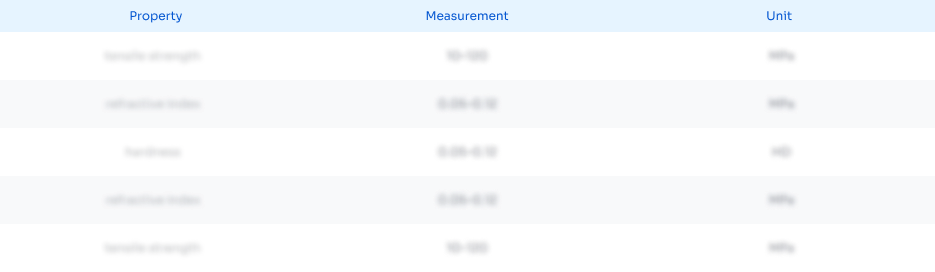
Abstract
Description
Claims
Application Information

- R&D
- Intellectual Property
- Life Sciences
- Materials
- Tech Scout
- Unparalleled Data Quality
- Higher Quality Content
- 60% Fewer Hallucinations
Browse by: Latest US Patents, China's latest patents, Technical Efficacy Thesaurus, Application Domain, Technology Topic, Popular Technical Reports.
© 2025 PatSnap. All rights reserved.Legal|Privacy policy|Modern Slavery Act Transparency Statement|Sitemap|About US| Contact US: help@patsnap.com