Tuning fork type piezoelectic oscillatory sheet, its mfg. method and piezoelectric device
A tuning-fork type piezoelectric and piezoelectric oscillation technology, which is applied in the manufacturing/assembly of piezoelectric/electrostrictive/magnetostrictive devices, piezoelectric devices/electrostrictive devices, and piezoelectric/electrostrictive devices, etc. It can solve problems such as the increase of natural frequency fluctuation value, the decrease of piezoelectric oscillator plate, and the unstable vibration characteristics.
- Summary
- Abstract
- Description
- Claims
- Application Information
AI Technical Summary
Problems solved by technology
Method used
Image
Examples
Embodiment Construction
[0054] Hereinafter, preferred embodiments of the present invention will be described in detail with reference to the accompanying drawings.
[0055] figure 1 A preferred embodiment of a crystal oscillator suitable for the present invention is schematically shown.
[0056] Such a crystal resonator 10 includes a package 13 having a base 11 and a cover 12 made of an insulating material, and a tuning-fork-shaped crystal oscillator piece 14 is hermetically packaged inside the package 13 . The base 11 has a substantially rectangular box shape in which a plurality of thin ceramic plates are laminated, and a tuning-fork-shaped crystal resonator piece 14 is attached to the bottom of a space defined inside. The cover 12 is formed of a rectangular thin plate made of an insulating material such as glass or ceramics, and is hermetically connected to the upper end surface of the base 11 by low-melting glass. In order to adjust the frequency to be able to irradiate the laser beam from the...
PUM
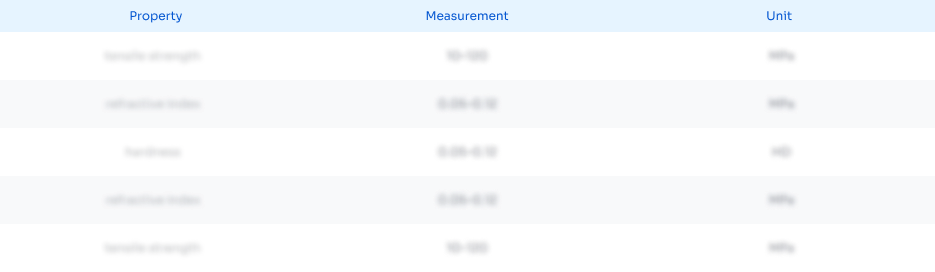
Abstract
Description
Claims
Application Information

- R&D Engineer
- R&D Manager
- IP Professional
- Industry Leading Data Capabilities
- Powerful AI technology
- Patent DNA Extraction
Browse by: Latest US Patents, China's latest patents, Technical Efficacy Thesaurus, Application Domain, Technology Topic, Popular Technical Reports.
© 2024 PatSnap. All rights reserved.Legal|Privacy policy|Modern Slavery Act Transparency Statement|Sitemap|About US| Contact US: help@patsnap.com