Method for synthesizing dimethyl carbonate by using urea and methanol and adopting heterogeneous catalyst
A heterogeneous catalyst, dimethyl carbonate technology, applied in the preparation of carbonate/haloformate, chemical instruments and methods, preparation of organic compounds, etc., can solve the problem of harsh reaction conditions, high price of raw gas, and product Solve problems such as difficult separation, and achieve the effect of safe reaction process, low raw material cost and simple process
- Summary
- Abstract
- Description
- Claims
- Application Information
AI Technical Summary
Problems solved by technology
Method used
Examples
Embodiment 1
[0019] Choose calcium carbonate as the precursor salt, weigh a certain amount of calcium carbonate in a high-temperature furnace, and calcinate the catalyst at 900°C, 0.1MPa, and air atmosphere for 2 hours to obtain a solid calcium oxide catalyst. Weigh 15 grams of urea, measure 20 milliliters of methanol, the molar ratio of methanol to urea is 2:1, put them into an autoclave, add 2 grams of CaO catalyst, rapidly heat from room temperature to 140 °C under magnetic stirring, keep for 3 hours, and then Heating to 190°C, constant temperature reaction for 5 hours, after the temperature dropped to room temperature, the reaction product was analyzed by gas chromatography, the results are listed in Table 1.
Embodiment 2
[0021] Choose calcium carbonate as the precursor salt, weigh a certain amount of calcium carbonate in a high-temperature furnace, and calcinate the catalyst at 900°C, 0.1MPa, and nitrogen atmosphere for 2 hours to obtain a solid calcium oxide catalyst. Weigh 15 grams of urea, measure 40 milliliters of methanol, the molar ratio of methanol to urea is 4:1, put them into an autoclave, and add 3 grams of CaO catalyst, rapidly heat from room temperature to 140 ° C under magnetic stirring, keep for 3 hours, and then Heating to 190°C, constant temperature reaction for 12 hours, after the temperature dropped to room temperature, the reaction product was analyzed by gas chromatography, the results are listed in Table 1.
Embodiment 3
[0023] Calcium carbonate was selected as the precursor salt, a certain amount of calcium carbonate was weighed in a high-temperature furnace, and the catalyst was calcined at 900° C., 0.1 MPa, and nitrogen atmosphere for 6 hours to obtain a solid calcium oxide catalyst. Weigh 7.5 grams of urea, measure 30 milliliters of methanol, the molar ratio of methanol to urea is about 8:1, put it into an autoclave, and add 4 grams of CaO catalyst, rapidly heat from room temperature to 150 ° C under magnetic stirring, and keep for 2 hours, Then heated to 220° C. and reacted at constant temperature for 6 hours. After the temperature dropped to room temperature, the reaction product was analyzed by gas chromatography. The results are listed in Table 1.
PUM
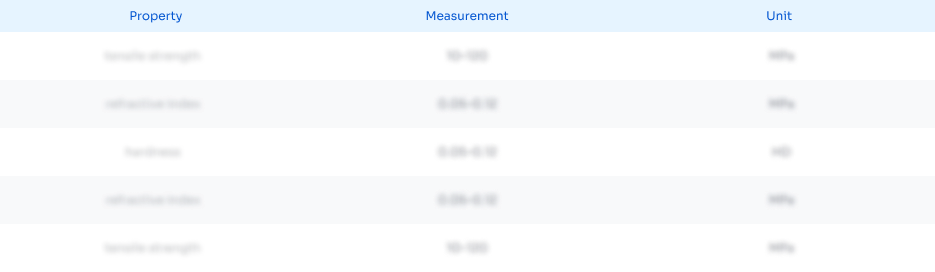
Abstract
Description
Claims
Application Information

- Generate Ideas
- Intellectual Property
- Life Sciences
- Materials
- Tech Scout
- Unparalleled Data Quality
- Higher Quality Content
- 60% Fewer Hallucinations
Browse by: Latest US Patents, China's latest patents, Technical Efficacy Thesaurus, Application Domain, Technology Topic, Popular Technical Reports.
© 2025 PatSnap. All rights reserved.Legal|Privacy policy|Modern Slavery Act Transparency Statement|Sitemap|About US| Contact US: help@patsnap.com