Synthetic fibre containing animal protein and its preparing method
A technology of synthetic fiber and protein, which is applied in the field of synthetic fiber containing animal protein and its preparation, and can solve the problems of poor uniformity of natural protein fiber, etc.
- Summary
- Abstract
- Description
- Claims
- Application Information
AI Technical Summary
Problems solved by technology
Method used
Examples
Embodiment 1
[0033] Select wool as raw material, first clean and pretreat the wool and add it to a mixed solution containing 1wt% sodium dodecylsulfate, 3wt% sodium bisulfite and 13wt% urea for dissolution; the dissolution temperature is 80°C, The dissolution time was 5 hours; the resulting solution was filtered to remove insoluble matter.
[0034] The keratin is separated and purified by salting-out method. Calcium chloride salt is added to the solution and stirred while adding until the keratin precipitates, then filtered and washed several times with water. Dissolve the separated and purified keratin with a sodium hydroxide alkaline solution under heating conditions. The initial pH value of the alkaline solution is 9.5, the initial heating temperature is 75°C, the temperature rises by 5°C per hour, and the pH value rises by 0.5 per hour . Dissolving time is 3-4 hours. The dissolved solution should be concentrated to 13-20 wt%, that is, a concentrated wool keratin solution can be obtai...
Embodiment 2
[0038] When producing keratin, pig hair is selected as raw material, and the pig hair is cleaned and pretreated before being added to a mixture containing 0.5wt% sodium octadecylsulfonate, 2.5wt% mercaptopropanol and 11wt% calcium chloride. Dissolving in the solution; the dissolving temperature is 40° C., and the dissolving time is 8 hours; the obtained solution is filtered to remove insoluble matter.
[0039] Keratin is separated and purified by dialysis. Put the filtered solution into a semi-permeable membrane, immerse it in distilled water, change the water several times in the middle, and the dialysis time is about 30 hours.
[0040] Concentrate the dialyzed solution to 13-15wt% to obtain concentrated porcine hair keratin solution.
[0041] The polyvinyl alcohol polymer (PVA) is dissolved in water, and the operating conditions are the same as in Example 1.
[0042] Mix the concentrated pig hair keratin solution and PVA solution in proportion, the addition ratio is: 40 part...
Embodiment 3
[0044] Rabbit hair is selected as raw material, the rabbit hair is cleaned and pretreated, and then added to a mixed solution containing 1.5wt% sodium dodecylsulfonate, 5.5wt% ammonium thioglycolate and 12wt% urea for dissolution; The temperature was 50°C, and the dissolution time was 7 hours; the resulting solution was filtered to remove insoluble matter.
[0045] Keratin is separated and purified by isoelectric point method. Adjust the isoelectric point of keratin protein to separate it from the solution, filter and wash it with sodium hydroxide alkaline solution with a pH value of 9-10, the dissolution time is 5 hours, and the dissolution temperature is 75°C-95°C , the solution after dissolving should be concentrated to 13-15 wt%, to obtain concentrated rabbit hair keratin solution.
[0046] The polyvinyl alcohol polymer (PVA) is dissolved in water, and the operating conditions are the same as in Example 1.
[0047] Mix the concentrated rabbit hair keratin solution and PV...
PUM
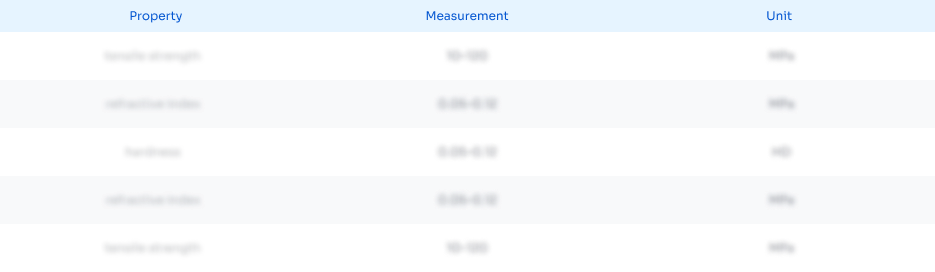
Abstract
Description
Claims
Application Information

- R&D Engineer
- R&D Manager
- IP Professional
- Industry Leading Data Capabilities
- Powerful AI technology
- Patent DNA Extraction
Browse by: Latest US Patents, China's latest patents, Technical Efficacy Thesaurus, Application Domain, Technology Topic, Popular Technical Reports.
© 2024 PatSnap. All rights reserved.Legal|Privacy policy|Modern Slavery Act Transparency Statement|Sitemap|About US| Contact US: help@patsnap.com