Method for preparing unsaturated carboxylic ester
A technology for saturated carboxylic acid esters and carboxylic acids, which is applied in the field of preparing unsaturated carboxylic acid esters, can solve the problems of reducing resin amount, resin outflow, pipeline blockage, etc., and achieves the effect of removing losses and preventing polymers.
- Summary
- Abstract
- Description
- Claims
- Application Information
AI Technical Summary
Problems solved by technology
Method used
Image
Examples
Embodiment 1
[0042] The esterification reaction of acrylic acid and n-butanol was carried out at a stirring speed of 40 rpm in a cylindrical reaction vessel with an inner diameter of 3100 mm and a straight body length of 3100 mm and a diameter of 1900 mm Faudler blades. As a catalyst for this reaction a volume of 15.5 m 3 (in a state soaked with water) of a cation exchange resin (manufactured by Misubishi Chemical Industry Co., Ltd., and sold under the trademark "Diaion PK 208"). The reaction was carried out under conditions of a reaction temperature (temperature of the reaction solution) of 80° C. and a reaction pressure of 20 kPa (absolute pressure). The reaction solution is heated with steam, and the steam is passed through a jacket covering 90% of the height of the straight body of the reactor. The pressure inside the jacket was 0.2 MPa (gauge pressure), and the temperature at the outer peripheral portion of the reaction vessel was about 133°C. The volume of the reaction solution is ...
Embodiment 2
[0047] Resin separation tank is installed in the reaction vessel of embodiment 1, and its internal diameter is 1700mm, and length is 2000mm, and when reaction is carried out, reaction solution is separated into the slurry that contains resin and clear liquid. The flow rate of the reaction solution sent from the reaction vessel to the resin separation tank is 112m 3 / h. 18m 3 / h flow out, and the slurry circulates back to the reaction vessel at a speed of 1.5m / sec. The slurry concentration in the slurry discharged from the resin separation tank was 25% by volume.
[0048] A stainless steel pipe with a diameter of 150 mm was used as a flow path for the slurry to circulate from the resin knockout tank to the reaction vessel. Since the radius of curvature of the bend formed on the pipeline is 600mm, there is no problem such as blockage inside the pipeline.
Embodiment 3
[0050] The esterification reaction of acrylic acid and 2-ethylhexyl alcohol utilizes a volume of 10m 3 (water-soaked state) of strongly acidic cation exchange resin (manufactured by Mitsubishi Chemical Industry Co., Ltd., and its sales trademark is "Diaion PK 208") at a reaction temperature (reaction solution temperature) of 85° C. and a reaction pressure of 10 kPa (absolute pressure) under conditions. The feed liquid entering the reaction vessel was preheated to 80°C with a preheater. The reaction solution was also heated by steam fed into a jacket fitted over the reaction vessel. The internal pressure of the jacket was 0.35 MPa (gauge pressure), and the temperature at the outer periphery of the reaction vessel was about 148°C. The speed at which the reaction solution is sent from the reaction vessel to the resin separation tank is 2 m / sec.
[0051] The supernatant is separated from the resin tank at a distance of 7m 3 The flow rate of / h flows out, and the slurry contain...
PUM
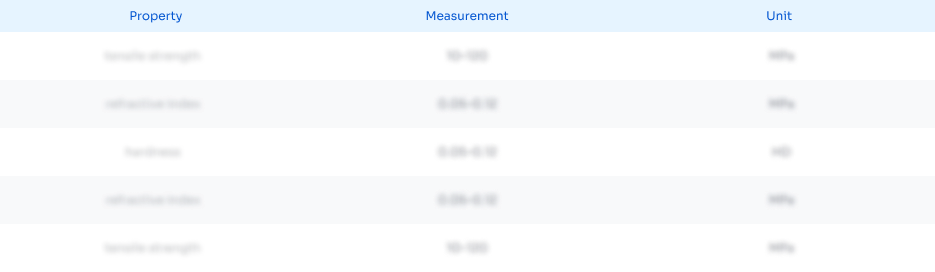
Abstract
Description
Claims
Application Information

- R&D Engineer
- R&D Manager
- IP Professional
- Industry Leading Data Capabilities
- Powerful AI technology
- Patent DNA Extraction
Browse by: Latest US Patents, China's latest patents, Technical Efficacy Thesaurus, Application Domain, Technology Topic, Popular Technical Reports.
© 2024 PatSnap. All rights reserved.Legal|Privacy policy|Modern Slavery Act Transparency Statement|Sitemap|About US| Contact US: help@patsnap.com