Process for preparing liquefied propane gas and gasoline with high octane value from plant fibres
A plant fiber and liquefied gas technology, which is applied in the preparation of liquid hydrocarbon mixtures and the petroleum industry, can solve the problems of high cost, complicated process, and lack of practical promotion and application, and achieve less impurities, extensive resources, and low cost. Effect
- Summary
- Abstract
- Description
- Claims
- Application Information
AI Technical Summary
Problems solved by technology
Method used
Examples
Embodiment 1
[0026] Take corn stalks, crush them into granules and mix them with auxiliary material anthracite, dry at 105°C to 115°C to remove internal moisture, put 100kg of dried straw and 22kg of anthracite into a vacuum retort at a temperature of 300°C to Gradient temperature rise at 500°C for cracking reaction, the reaction time is 2.5 minutes, and 1m 3 Mixed combustible gas, 30% of which is propane gas and 70% is CO gas.
[0027] CO was separated at one time by PSA four-bed pressure swing adsorption method. Process operating conditions: raw material gas temperature is 50-80, pressure is 0.1-0.5Mpa, CO decompression recovery pressure is 6-13Kpa, adsorption cycle is 12-20min, flushing gas ratio (flushing amount / raw material amount) is 0.3-0.7. The purity of the CO product is 98-99%, and the recovery rate is greater than 80%.
[0028] 60% of the separated CO is added with excess steam at a temperature of 400-480°C under the action of a catalyst to react to generate hydrogen and carbo...
PUM
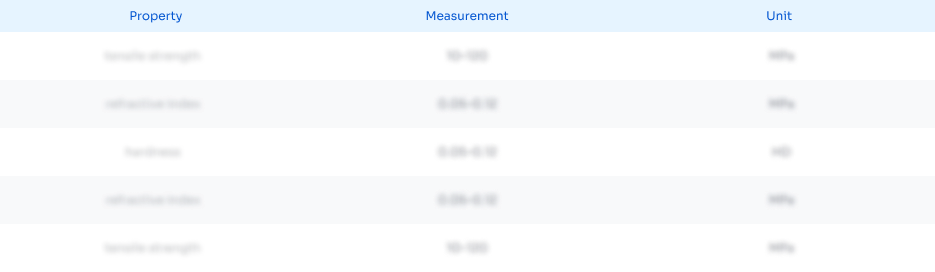
Abstract
Description
Claims
Application Information

- R&D Engineer
- R&D Manager
- IP Professional
- Industry Leading Data Capabilities
- Powerful AI technology
- Patent DNA Extraction
Browse by: Latest US Patents, China's latest patents, Technical Efficacy Thesaurus, Application Domain, Technology Topic, Popular Technical Reports.
© 2024 PatSnap. All rights reserved.Legal|Privacy policy|Modern Slavery Act Transparency Statement|Sitemap|About US| Contact US: help@patsnap.com