Preparation of high-purity titanium biboride ceramic micropowder by using self-spreading high-temp. reduction synthesis process
A self-propagating high-temperature, titanium diboride technology, applied in the field of refractory compounds and their solid-phase synthesis, can solve the problems of long time, coarse product particle size, large powder particle size, etc., achieve low energy consumption and time consumption, and simple process , the effect of fine grain
- Summary
- Abstract
- Description
- Claims
- Application Information
AI Technical Summary
Problems solved by technology
Method used
Examples
example 1
[0015] Example 1: 27 grams of TiO 2 Powder (≤80μm), 26g B 2 o 3 Mg powder (≤120μm), 47 grams of Mg powder (≤200μm) are fully mixed. The mixed sample is pressed into a block blank, put into a self-propagating high-temperature synthesis reactor, and under the protection of argon gas at normal temperature and pressure, the surface of the sample is ignited with a tungsten wire or an electric arc. The combustion wave spreads rapidly. At this time, the combustion temperature of the sample is 1800-2000°C, and the combustion reaction is completed within 1-2 minutes. After the sample was completely cooled, it was placed in a ball mill for ball milling for 2 hours. The obtained powder was put into a reaction kettle, 10 liters of hydrochloric acid with a concentration of 1 mol / l was added and stirred continuously, acid washed at 50° C. for 4 hours, filtered and dried. The composition of the obtained micropowder is: Ti68.2wt%, B30.1wt%, O0.5wt%, N0.1wt%, Mg0.1wt%, and the average part...
example 2
[0016] Example 2: 29 grams of TiO 2 Powder (≤80μm), 26g B 2 o 3 Mg powder (≤120μm), 45 grams of Mg powder (≤200μm) are fully mixed. The mixed sample is pressed into a block blank, put into a self-propagating high-temperature synthesis reactor, and under the protection of argon gas at normal temperature and pressure, the surface of the sample is ignited with a tungsten wire or an electric arc. The combustion wave spreads rapidly. At this time, the combustion temperature of the sample is 2000-2200°C, and the combustion reaction is completed within 1-2 minutes. After the sample was completely cooled, it was placed in a ball mill for ball milling for 2 hours. The obtained powder was put into a reaction kettle, 20 liters of sulfuric acid with a concentration of 0.5 mol / l was added and stirred continuously, acid washed at 50° C. for 6 hours, filtered and dried. The composition of the obtained micropowder is: Ti68.8wt%, B30.35wt%, O0.7wt%, N0.1wt%, Mg0.05wt%, and the average part...
example 3
[0017] Example 3: 29 grams of TiO 2 Powder (≤80μm), 28g B 2 o 3 Mg powder (≤1200μm), 43 grams of Mg powder (≤200μm) are fully mixed. The mixed sample is pressed into a block blank, put into a self-propagating high-temperature synthesis reactor, and under the protection of argon gas at normal temperature and pressure, the surface of the sample is ignited with a tungsten wire or an electric arc. The combustion wave spreads rapidly. At this time, the combustion temperature of the sample is 1700-1900°C, and the combustion reaction is completed within 1-2 minutes. After the sample was completely cooled, it was placed in a ball mill for ball milling for 2 hours. The obtained powder was put into a reaction kettle, 10 liters of hydrochloric acid with a concentration of 1 mol / l was added and stirred continuously, acid washed at 50° C. for 4 hours, filtered and dried. The composition of the obtained micropowder is: Ti67.87wt%, B31.3wt%, O0.6wt%, N0.1wt%, Mg0.13wt%, and the average p...
PUM
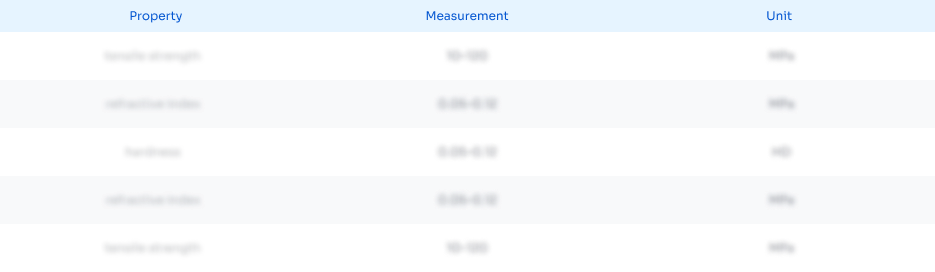
Abstract
Description
Claims
Application Information

- Generate Ideas
- Intellectual Property
- Life Sciences
- Materials
- Tech Scout
- Unparalleled Data Quality
- Higher Quality Content
- 60% Fewer Hallucinations
Browse by: Latest US Patents, China's latest patents, Technical Efficacy Thesaurus, Application Domain, Technology Topic, Popular Technical Reports.
© 2025 PatSnap. All rights reserved.Legal|Privacy policy|Modern Slavery Act Transparency Statement|Sitemap|About US| Contact US: help@patsnap.com