Substrate for printed circuitboard distributing
A printed circuit and wiring technology, which is applied to printed circuit components, circuit devices, electrical components, etc., can solve the problems of reduced film strength, reduced film formation, and difficulty in forming, so as to prevent damage to magnetic permeability performance and durability. Excellent, the effect of preventing stringing
- Summary
- Abstract
- Description
- Claims
- Application Information
AI Technical Summary
Problems solved by technology
Method used
Image
Examples
Embodiment 1
[0208] 【Substrate】
[0209] One side surface of a 50 μm thick polyimide sheet was subjected to oxygen plasma treatment (output power 300W), and it was used as a base material for later use.
[0210] 【Formation of Adhesive Layer】
[0211] The components in the following Table 1 were mixed and stirred for 5 hours in an atmosphere with a relative humidity of 30%, whereby the hydrolysis reaction was carried out by the moisture in the atmosphere to generate a titanium sol solution.
[0212] Element
g
Isopropanol
2-Ethylhexanoic acid
284
600
144
[0213] The surface treated with oxygen plasma was exposed, and the above-mentioned polyimide sheet masked on the opposite side was immersed in the above-mentioned titanium sol solution, and then lifted at a speed of 0.5 cm / min, thereby forming a titanium dioxide sol with a thickness of about 10 nm. Treat the membrane.
[0214] Then, the polyimide sheet was heated ...
Embodiment 2
[0224] In the same manner as in Example 1, except that the adhesive layer is formed by the following steps, on the surface of the polyimide sheet as the substrate through oxygen plasma treatment, a silicon dioxide titanium dioxide adhesive layer is laminated with 12 The electromagnetic wave absorbing layer of the layer-by-layer structure is made into a printed circuit board.
[0225] [Formation of Adhesive Layer]
[0226] The components in the following Table 2 were mixed, stirred for 5 hours in an atmosphere with a relative humidity of 30%, and hydrolyzed by the moisture in the atmosphere to generate a silicon-titanium sol solution.
[0227] Element
g
tetrabutyl orthosilicate
Isopropanol
2-Ethylhexanoic acid
100
86
600
144
[0228] The surface treated with oxygen plasma is exposed, and the above-mentioned polyimide sheet masked on the opposite side is immersed in the above-mentioned silicon-ti...
Embodiment 3
[0231] Using a glass epoxy resin substrate with a thickness of 500 μm as the base material, except that the oxygen plasma treatment on its surface is omitted, the others are the same as in Example 1. On one side surface of the glass epoxy resin substrate, through a titanium dioxide adhesive layer, Electromagnetic wave absorbing layers having a laminated structure of 12 layers were laminated, thereby producing a printed circuit board.
PUM
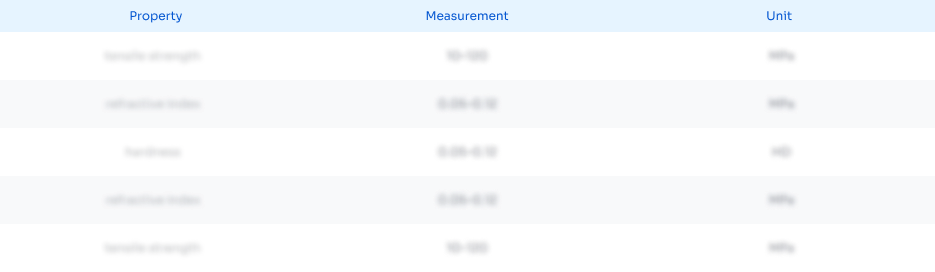
Abstract
Description
Claims
Application Information

- Generate Ideas
- Intellectual Property
- Life Sciences
- Materials
- Tech Scout
- Unparalleled Data Quality
- Higher Quality Content
- 60% Fewer Hallucinations
Browse by: Latest US Patents, China's latest patents, Technical Efficacy Thesaurus, Application Domain, Technology Topic, Popular Technical Reports.
© 2025 PatSnap. All rights reserved.Legal|Privacy policy|Modern Slavery Act Transparency Statement|Sitemap|About US| Contact US: help@patsnap.com