Method for production of high-purity concentrated magnesium chloride solution
A solution and slurry technology, applied in the field of preparing magnesium chloride solution, can solve the problems of expensive installation and maintenance of ion exchange columns, obstacles to magnesium production, etc.
- Summary
- Abstract
- Description
- Claims
- Application Information
AI Technical Summary
Problems solved by technology
Method used
Image
Examples
Embodiment 1
[0058] This example shows that when all the conditions of the process of the present invention are met, a substantially pure magnesium chloride solution having less than 1 ppm of any contaminant in the solution can be prepared.
[0059] Serpentine tailings (composition: 23% Mg; 5% Fe; 0.0593% Mn and 0.21% Ni) were continuously fed into the first leaching reactor at a rate of 140kg / h. Concentrated hydrochloric acid (33%), circulating hydrochloric acid (4-7%) and circulating washing water (30-60g / l Mg) are also continuously fed into the first reactor at flow rates of 218l / h, 56l / h and 100l / h, respectively. About 68% of the magnesium was extracted in the first leach reactor and 72% in the second leach reactor. The total residence time in both reactors was 120 minutes. The unheated temperature of the leaching reactor was 80-85°C. Magnesium oxide slurry (30wt%) was fed into the first neutralization reactor together with chlorine gas, the pH value was maintained at 1.8, and the po...
Embodiment 2
[0061] This example shows that when the potential value in the third neutralization reactor is unsuitable, the concentration of manganese is significantly higher than 1 ppm.
[0062] Serpentine tailings (composition: 23% Mg; 5% Fe; 0.0593% Mn and 0.21% Ni) were continuously fed into the first leaching reactor at a rate of 165 kg / h. Under these conditions, the circuit will operate at 120% of nominal flow. Concentrated hydrochloric acid (33%), circulating hydrochloric acid (4-7%) and circulating washing water (30-60g / l Mg) were also continuously fed into the first reactor at flow rates of 263l / h, 56l / h and 133l / h, respectively. The total residence time in both reactors was 100 minutes. About 68% of the magnesium was extracted in the first leach reactor and 74% in the second leach reactor. Magnesium oxide slurry (30wt%) was fed into the first neutralization reactor together with chlorine gas, the pH value was maintained at 1.7, and the potential was about +246mV (Ag-AgCl). Add...
Embodiment 3
[0064] The results in this example are obtained because some parameters in the method of the present invention are not within the specified range. As shown, when unfavorable pH and potential values are used, the nickel and iron concentrations are above 1 ppm.
[0065] Other conditions are the same as in Examples 1 and 2, only the acid / ore ratio used in the leaching process is 0.73. Serpentine tailings (composition: 22.8% Mg; 8.1% Fe; 0.0516% Mn and 0.21% Ni) are continuously fed into the first leaching reactor at a flow rate of 146kg / h, while 33% hydrochloric acid is added at 240l / h, 75l / h Add circulating hydrochloric acid (4-7%) and 82 l / h add circulating washing water (30-60 g / lMg). About 71% of the magnesium was extracted in the first leach reactor and 81% of the magnesium was extracted in the second leach reactor. The final solution from the last neutralization reactor contained an average concentration of 91.5 g / l Mg (28.7% MgCl 2 ). The average concentration is 1.5...
PUM
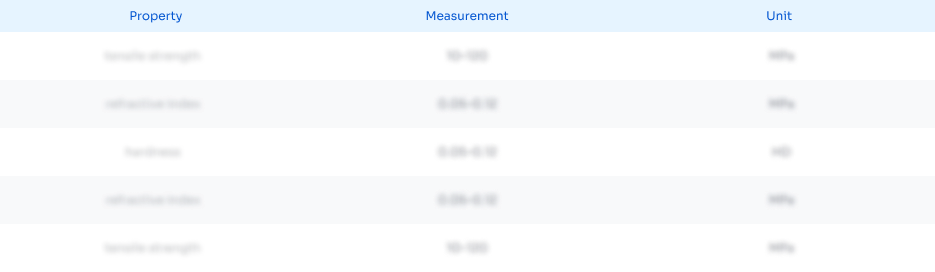
Abstract
Description
Claims
Application Information

- R&D
- Intellectual Property
- Life Sciences
- Materials
- Tech Scout
- Unparalleled Data Quality
- Higher Quality Content
- 60% Fewer Hallucinations
Browse by: Latest US Patents, China's latest patents, Technical Efficacy Thesaurus, Application Domain, Technology Topic, Popular Technical Reports.
© 2025 PatSnap. All rights reserved.Legal|Privacy policy|Modern Slavery Act Transparency Statement|Sitemap|About US| Contact US: help@patsnap.com