Aromatic multi-texture microporous thermoplastic resin wood-imitating materials and wood texture forming process
A thermoplastic resin and imitation wood material technology, applied in the field of polymer imitation wood material composition, can solve the problems of degumming and peeling, serious color difference, easy fading, etc., achieve natural and delicate wood grain, slow release of aroma, and good plasticizing effect Effect
- Summary
- Abstract
- Description
- Claims
- Application Information
AI Technical Summary
Problems solved by technology
Method used
Examples
Embodiment Construction
[0010] In the present invention, except main material, all the other fillers, processing aids, coloring agents, flavor enhancers etc. are all specifically taken according to the required characteristics of imitation wood products.
[0011] For example: (the following are all in parts by weight)
[0012] Gradually heat and mix 100 parts of polyvinyl chloride and 40 parts of light calcium carbonate. When the temperature rises to about 35-40°C, add 0.5 parts of calcium stearate, 3 parts of zinc oxide, 2 parts of magnesium oxide, and 0.4 parts of polyethylene wax , 0.2 parts of stearic acid, 0.5 parts of azodicarbonamide, 0.01 parts of deep chrome yellow, 0.002 parts of brilliant red, 0.03 parts of light chrome yellow, 3 parts of carbon black, 0.003 parts of brilliant yellow, 5 parts of chlorinated polyethylene , zinc dibutyldithiocarbamate: 0.2 parts, bisfumarate: 0.2 parts, titanium dioxide: 2 parts; 4 parts of dioctyl formate participate in stirring, add 6 parts of ZB530 foami...
PUM
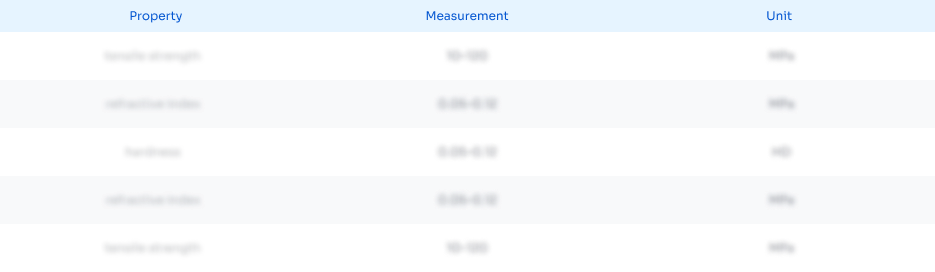
Abstract
Description
Claims
Application Information

- Generate Ideas
- Intellectual Property
- Life Sciences
- Materials
- Tech Scout
- Unparalleled Data Quality
- Higher Quality Content
- 60% Fewer Hallucinations
Browse by: Latest US Patents, China's latest patents, Technical Efficacy Thesaurus, Application Domain, Technology Topic, Popular Technical Reports.
© 2025 PatSnap. All rights reserved.Legal|Privacy policy|Modern Slavery Act Transparency Statement|Sitemap|About US| Contact US: help@patsnap.com