Oxygen enrichment combustion-supporting method for float glass melter
An oxygen-enriched combustion-supporting, float glass technology, which is applied in glass production, glass furnace equipment, glass manufacturing equipment, etc., can solve the problems that affect the continuous implementation, restrict the exploration experiment of oxygen-enriched combustion-supporting technology, and the pressure fluctuation of nitrogen supply is too large, etc. To achieve a reasonable distribution, to avoid local overheating of the roof temperature, and to reduce fuel consumption
- Summary
- Abstract
- Description
- Claims
- Application Information
AI Technical Summary
Problems solved by technology
Method used
Image
Examples
Embodiment Construction
[0009] A method for oxygen-enriched combustion in a float glass melting furnace according to the present invention, such as figure 1 , figure 2 As shown, the purifier of the air separation nitrogen unit and the oxygen-enriched air from the fractionation tower are respectively connected to the buffer storage tank at normal pressure. Float joint workshop, after entering the workshop, the oxygen-enriched air main pipe is divided into two routes, respectively controlled by a pneumatic cut-off valve (synchronized with the combustion air), and led to both sides of the regenerator of the glass melting furnace, and then along 1 # ,2 # The center line of the small furnace leads to a branch pipe, and a control valve is set on the branch pipe, and then the oxygen-enriched nozzle is introduced into the soot cleaning door of the regenerator.
[0010] In order to keep the nitrogen production system unaffected and maintain a stable nitrogen supply, an atmospheric pressure buffer storage t...
PUM
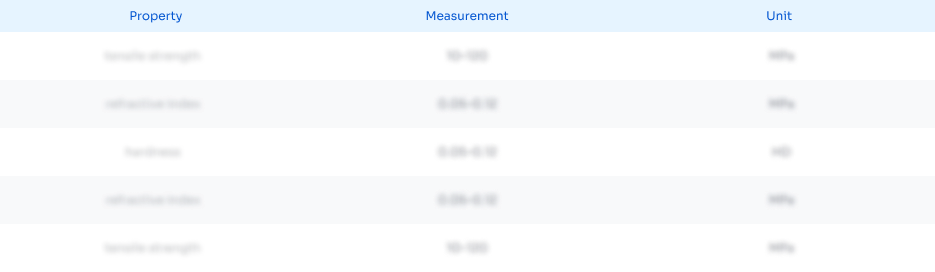
Abstract
Description
Claims
Application Information

- R&D Engineer
- R&D Manager
- IP Professional
- Industry Leading Data Capabilities
- Powerful AI technology
- Patent DNA Extraction
Browse by: Latest US Patents, China's latest patents, Technical Efficacy Thesaurus, Application Domain, Technology Topic, Popular Technical Reports.
© 2024 PatSnap. All rights reserved.Legal|Privacy policy|Modern Slavery Act Transparency Statement|Sitemap|About US| Contact US: help@patsnap.com