Electric furnace with insulated electrode and process for producing molten metals
A process method and electrode technology, which are used in electric furnaces, electric furnace heating, ohmic resistance electrodes, etc.
- Summary
- Abstract
- Description
- Claims
- Application Information
AI Technical Summary
Problems solved by technology
Method used
Image
Examples
example 1
[0111] A computer simulation operation consisted of a feed mixture containing 2000 lbs of scrap iron, 100 lbs of wood chips, 85 lbs of coal, 20 lbs of coke and 75 lbs quartzite. The planned input power of the electric furnace is 50,000 kilowatts. The simulated scrap feed consisted of the following: 40% shredded automotive steel; 15% remelt; 15% #1 steel scrap; 20% cast iron filings; 5% tin plate / can; . The feed mixture has a calculated alloy composition with balance iron: 2.5% silicon; 3.85% carbon; 0.40% manganese; 0.10% chromium; 0.15% nickel; 0.15% copper; 0.01% sulfur; 0.05% phosphorous Matter; 0.03% tin, here, each percentage is by weight.
[0112] The planned synthetic iron product exiting the furnace had the following composition with balancing impurities: 92.5% iron content; 3.85% carbon content; 2.50% silicon content by weight. The calculated energy consumption is 650 kWh per ton of ferroalloy.
PUM
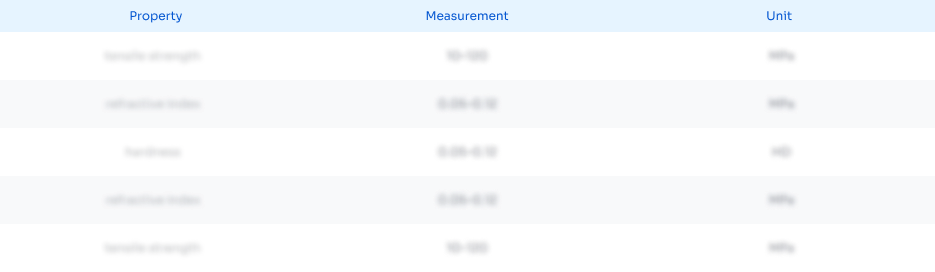
Abstract
Description
Claims
Application Information

- Generate Ideas
- Intellectual Property
- Life Sciences
- Materials
- Tech Scout
- Unparalleled Data Quality
- Higher Quality Content
- 60% Fewer Hallucinations
Browse by: Latest US Patents, China's latest patents, Technical Efficacy Thesaurus, Application Domain, Technology Topic, Popular Technical Reports.
© 2025 PatSnap. All rights reserved.Legal|Privacy policy|Modern Slavery Act Transparency Statement|Sitemap|About US| Contact US: help@patsnap.com