Method for production of slide fastener or stringers thereof
A zipper and half-edge technology, applied in clothing, metal material coating process, fasteners, etc., can solve the problems of destroying the uniformity of chemical polishing, increasing the cost of raw materials and required energy, and material deterioration.
- Summary
- Abstract
- Description
- Claims
- Application Information
AI Technical Summary
Problems solved by technology
Method used
Image
Examples
Embodiment 1
[0068] A slide fastener half having a copper alloy joining member composed of 85% Cu and 15% Zn was acid-treated by immersing it in an acid treatment solution kept at 30° C. for 2 minutes.
[0069]An acidic aqueous solution containing 1 g / l polyoxyethylene oleyl ether as a surfactant, 80 g / l hydrogen peroxide, 20 g / l sulfuric acid, 0.5 g / l phosphoric acid and 20 g / l methanol was used as an acidic treatment solution.
[0070] Then, remove the acid treatment solution contained in the zipper tape by vacuum dehydration, so as to facilitate water washing in the next step.
[0071] Then as a washing step, the zipper halves are vigorously sprayed with water, immediately vacuum-dried, immersed in water, and immediately vacuum-dried again.
[0072] In order to thoroughly remove the acidic treatment liquid contained in the fastener tape, the above water washing steps consisting of spraying, dehydration, dipping and dehydration were repeated three times.
[0073] The surface condition o...
Embodiment 2
[0080] In the same manner as in Example 1, a slide fastener half having a copper alloy joining member composed of 85% Cu and 15% Zn was acid-treated by immersing it in an acid treatment solution kept at 30° C. for 2 minutes, and then washed with water. Wherein the acid treatment liquid used is identical with that used in embodiment 1. The water washing step was performed in the same manner as in Example 1.
[0081] Next, the acid-treated slide fastener half was immersed in an aqueous solution containing 1 g / l of 1,1,1-benzotriazole at room temperature for 30 seconds to perform antirust treatment.
[0082] Then, the antirust slide fastener half was dehydrated, placed in a drying device, and dried therein by blowing hot air at 130° C. for 3 minutes.
[0083] Subsequently, an acryl-urethane based clear paint was applied to the outer surface of the engaging member on the half of the slide fastener with a roller, and the paint layer was dried with hot air at 110° C., whereby a cle...
PUM
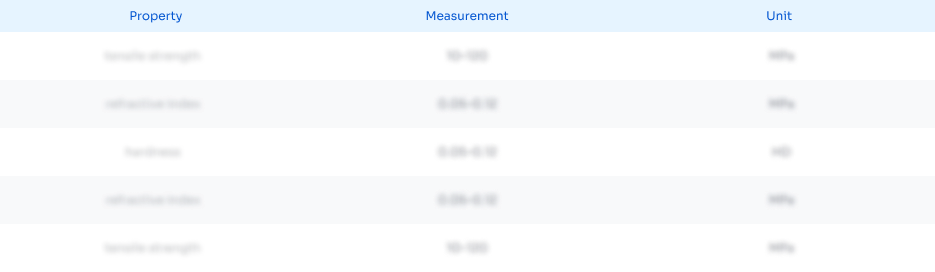
Abstract
Description
Claims
Application Information

- Generate Ideas
- Intellectual Property
- Life Sciences
- Materials
- Tech Scout
- Unparalleled Data Quality
- Higher Quality Content
- 60% Fewer Hallucinations
Browse by: Latest US Patents, China's latest patents, Technical Efficacy Thesaurus, Application Domain, Technology Topic, Popular Technical Reports.
© 2025 PatSnap. All rights reserved.Legal|Privacy policy|Modern Slavery Act Transparency Statement|Sitemap|About US| Contact US: help@patsnap.com