Pre-baked anode anti-oxidation coating capable of reducing energy consumption of aluminum electrolysis cell and preparation and application methods of pre-baked anode anti-oxidation coating
A technology of anti-oxidation coating and pre-baked anode, applied in coating and other directions, can solve the problems of different power consumption and no energy saving effect, and achieve the effect of reducing power consumption, preventing oxidation and peeling, and reducing resistance
- Summary
- Abstract
- Description
- Claims
- Application Information
AI Technical Summary
Problems solved by technology
Method used
Image
Examples
Embodiment 1
[0037] 1000kg of pre-baked anodic anti-oxidation coating for reducing the energy consumption of aluminum electrolytic cells, the components of the coating and their mass percentages are:
[0038] Alumina, accounting for 45% of the total mass of the coating, a total of 450kg;
[0039] Alkali metal grain boundary fusion agent, accounting for 3% of the total mass of the coating, a total of 30kg; the alkali metal grain boundary fusion agent includes plagioclase ore powder, albite and sodium fluorosilicate, respectively accounting for the total alkali metal grain boundary fusion agent. 55%, 35% and 10% of the mass, namely 16.5kg of plagioclase ore powder, 10.5kg of albite and 3kg of sodium fluorosilicate;
[0040] Reinforcing agent, accounting for 30% of the total mass of the coating, a total of 300kg; the reinforcing agent is silica sol with a solid content of 10%;
[0041] Coupling agent, accounting for 0.799% of the total mass of the coating, a total of 7.99kg; the coupling age...
Embodiment 2
[0051] 1000kg of pre-baked anodic anti-oxidation coating for reducing the energy consumption of aluminum electrolytic cells, the components of the coating and their mass percentages are:
[0052] Alumina, accounting for 50% of the total mass of the coating, a total of 500kg;
[0053] Alkali metal grain boundary fusion agent, accounting for 2% of the total mass of the coating, a total of 20kg; the alkali metal grain boundary fusion agent includes plagioclase ore powder, albite and sodium fluorosilicate, respectively accounting for the total alkali metal grain boundary fusion agent. 55%, 40% and 5% of the mass, namely 11kg of plagioclase ore powder, 5kg of albite and 1kg of sodium fluorosilicate;
[0054] Reinforcing agent, accounting for 25% of the total mass of the coating, a total of 250kg; the reinforcing agent is silica sol with a solid content of 10%;
[0055] Coupling agent, accounting for 0.3% of the total mass of the coating, a total of 3kg; the coupling agent adopts D...
Embodiment 3
[0065] 1000kg of pre-baked anodic anti-oxidation coating for reducing the energy consumption of aluminum electrolytic cells, the components of the coating and their mass percentages are:
[0066] Alumina, accounting for 47% of the total paint mass, a total of 470kg;
[0067] Alkali metal grain boundary fusion agent, accounting for 2.5% of the total mass of the coating, a total of 25kg; the alkali metal grain boundary fusion agent includes plagioclase ore powder, albite and sodium fluorosilicate, respectively accounting for the total alkali metal grain boundary fusion agent. 60%, 35% and 5% of the mass, namely 15kg of plagioclase ore powder, 8.75kg of albite and 1.25kg of sodium fluorosilicate;
[0068] Reinforcing agent, accounting for 28% of the total mass of the coating, a total of 280kg; the reinforcing agent is silica sol with a solid content of 10%;
[0069] Coupling agent, accounting for 0.5% of the total mass of the coating, a total of 5kg; the coupling agent adopts DL...
PUM
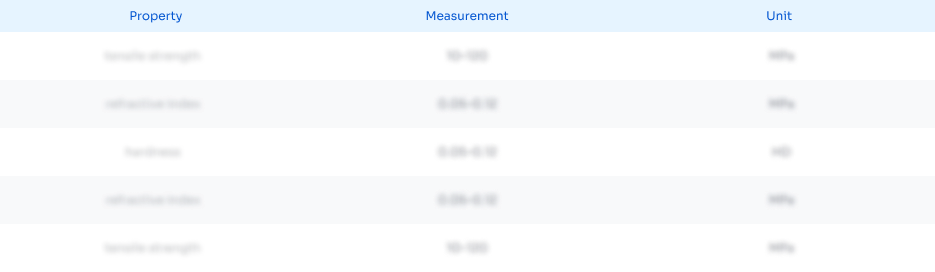
Abstract
Description
Claims
Application Information

- R&D
- Intellectual Property
- Life Sciences
- Materials
- Tech Scout
- Unparalleled Data Quality
- Higher Quality Content
- 60% Fewer Hallucinations
Browse by: Latest US Patents, China's latest patents, Technical Efficacy Thesaurus, Application Domain, Technology Topic, Popular Technical Reports.
© 2025 PatSnap. All rights reserved.Legal|Privacy policy|Modern Slavery Act Transparency Statement|Sitemap|About US| Contact US: help@patsnap.com