Workpiece positioning mechanism of laser cutting machine
A laser cutting machine and positioning mechanism technology, applied in laser welding equipment, manufacturing tools, metal processing equipment, etc., can solve the problems of workpiece deformation, cutting size error, unstable fixation, etc., to improve quality, improve stability, reduce effect of contact
- Summary
- Abstract
- Description
- Claims
- Application Information
AI Technical Summary
Problems solved by technology
Method used
Image
Examples
specific Embodiment 1
[0037] see Figure 1-11 As shown, the present invention is a workpiece positioning mechanism of a laser cutting machine, comprising two sets of clamping assemblies 1 arranged oppositely; the two clamping assemblies 1 clamp the workpiece 2; the clamping assembly 1 includes a clamping frame 3; The frame 3 is symmetrically slidably fitted with a clamping plate 4; the clamping plate 4 at the bottom is fixedly connected with a mounting frame 5 by fastening bolts; the installation frame 5 is slidably fitted with a transmission assembly 6; A sliding rod 8 is symmetrically and fixedly connected to the side of the fixing plate 7; the transmission assembly 6 includes two parallel mounting platforms 9; a mounting plate 10 is symmetrically and fixedly connected between the two mounting platforms 9; Mounting holes 12 are symmetrically opened on the side of the table 9; the mounting holes 12 are slidingly matched with the sliding rod 8; one end of the rotating shaft of the driving roller 11...
specific Embodiment 2
[0039] On the basis of the specific embodiment 1, the differences of this embodiment are:
[0040] like figure 1 , 5 -7 and Figure 11 As shown, the clamping frame 3 includes a C-shaped plate 19; the two ends of the C-shaped plate 19 are symmetrically opened with limit channels 20; the two sides of the limit channel 20 are symmetrically opened with guide channels 21; The slide plate 22; the slide plate 22 is slidingly matched with the guide channel 21; the side surface of the slide plate 22 is fixedly connected with a gear plate 23; the gear plate 23 is slidingly matched with the limit channel 20; The side of the 19 is rotatably matched with the drive roller 25; the side of the C-shaped plate 19 is located on both sides of the drive roller 25 and is fixedly connected to the connecting plate 26; the side of the connecting plate 26 is fixedly connected with a first rotating shaft 27; ; The gear ring 28 meshes with the gear plate 23 .
[0041] A first conical tooth 29 is fixe...
specific Embodiment 3
[0043] On the basis of the second specific embodiment, the difference of this embodiment lies in:
[0044] like Figure 7-8 As shown, the other side of the clamping plate 4 is provided with anti-skid lines 35; the adjacent sides of the clamping plate 4 are symmetrically provided with first threaded holes 36; the C-shaped plate 19 is fixed on the clamping plate 4 by fastening bolts; A diagonal brace 37 is fixedly connected to the bottom surface of the plate 19;
[0045] A specific application of this embodiment is as follows: the opening of the anti-skid grooves 35 increases the friction between the workpiece 2 and the clamping plate 4 and improves the clamping stability of the clamping plate 4; stability.
PUM
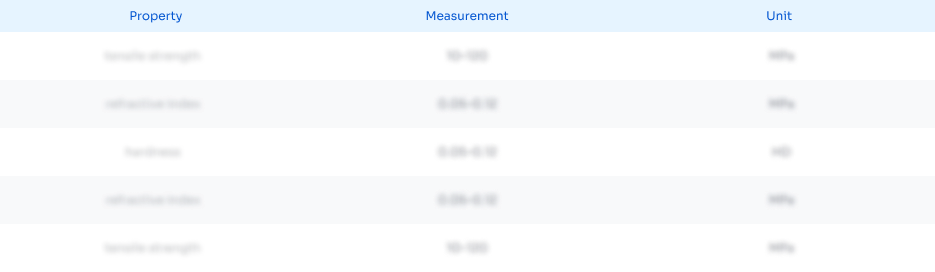
Abstract
Description
Claims
Application Information

- R&D
- Intellectual Property
- Life Sciences
- Materials
- Tech Scout
- Unparalleled Data Quality
- Higher Quality Content
- 60% Fewer Hallucinations
Browse by: Latest US Patents, China's latest patents, Technical Efficacy Thesaurus, Application Domain, Technology Topic, Popular Technical Reports.
© 2025 PatSnap. All rights reserved.Legal|Privacy policy|Modern Slavery Act Transparency Statement|Sitemap|About US| Contact US: help@patsnap.com