Drill jumbo and drill boom system
A technology for drilling booms and booms, which is applied in the field of rock drilling rigs and drilling boom systems. It can solve the problems of increasing the weight of the boom end, inconvenient operation of the boom system, and bulky boom system, and achieves output torque and braking torque. The effect of low size requirements, weight reduction, and increased flexibility
- Summary
- Abstract
- Description
- Claims
- Application Information
AI Technical Summary
Problems solved by technology
Method used
Image
Examples
Embodiment 1
[0038] In this embodiment, the telescopic boom adopts a three-stage boom body as an example to illustrate the folding and unfolding method. refer to Figure 1 to Figure 3 , the drill boom system includes a connecting seat 5, a first boom 1, a second boom 11 and a third boom 16, the first boom 1, the second boom 11 and the third boom 16 are closed in a "Z" fold. The drive link mechanism includes a first link 9, a second link 10, a third link 13, a fourth link 14, a first deployment cylinder 8 and a second deployment cylinder 12; the first link 9, the second link The rod 10 and the first deployment cylinder 8 are used to drive the second boom 11 to fold and unfold relative to the first boom 1, and the third link 13, the fourth link 14 and the second deployment cylinder 12 are used to drive the third arm The frame 16 is folded and unfolded relative to the second boom frame 11 , and the telescopic boom frame is connected to the third boom frame 16 .
[0039]Specifically, the fi...
Embodiment 2
[0045] refer to Figure 4 and Figure 5 , in the drill boom system provided in this embodiment, the folding boom still adopts the form of the first boom 1, the second boom 11 and the second boom 11 being hinged in sequence, and the driving link mechanism includes the first link 9, The second link 10, the third link 13, the fourth link 14, the first deployment cylinder 8 and the second deployment cylinder 12; the first link 9, the second link 10 and the first deployment cylinder 8 are used to drive The second boom 11 is folded and unfolded relative to the first boom 1 . The third link 13 , the fourth link 14 and the second deployment cylinder 12 are used to drive the third boom 16 to fold and unfold relative to the second boom 11 . , the telescopic boom is connected to the third boom 16 . The first link 9 and the third link 13 are both triangular links. The difference is that the first link 9 is hinged to the second boom 11, the second link 10 is hinged to the first boom 1, a...
Embodiment 3
[0047] refer to Image 6 In this embodiment, on the basis of Embodiment 1, the positions of the third link 13, the fourth link 14 and the second deployment cylinder 12 that drive the folding and unfolding of the second boom 11 and the third boom 16 are adjusted, After the folding boom is folded, the second unfolding cylinder 12 is located below the second boom 11 .
PUM
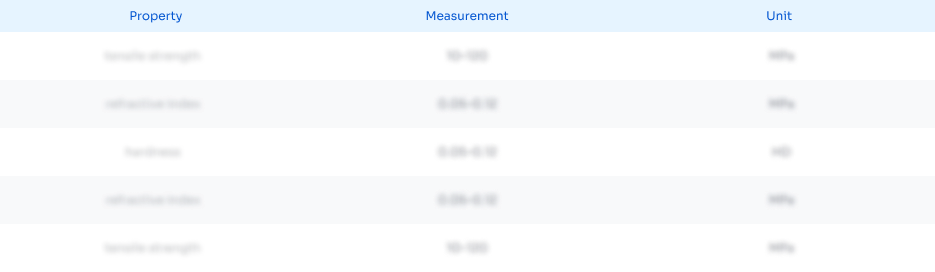
Abstract
Description
Claims
Application Information

- Generate Ideas
- Intellectual Property
- Life Sciences
- Materials
- Tech Scout
- Unparalleled Data Quality
- Higher Quality Content
- 60% Fewer Hallucinations
Browse by: Latest US Patents, China's latest patents, Technical Efficacy Thesaurus, Application Domain, Technology Topic, Popular Technical Reports.
© 2025 PatSnap. All rights reserved.Legal|Privacy policy|Modern Slavery Act Transparency Statement|Sitemap|About US| Contact US: help@patsnap.com