Base coordinate system creation method for numerical control equipment group collaborative production line installation
A technology of base coordinate system and numerical control equipment, which is applied in the field of base coordinate system creation for the collaborative production line installation of numerical control equipment groups, can solve the problems of poor position accuracy, low installation efficiency, long heading span, etc.
- Summary
- Abstract
- Description
- Claims
- Application Information
AI Technical Summary
Problems solved by technology
Method used
Image
Examples
Embodiment 1
[0035] refer to Figure 1 to Figure 5 , this embodiment provides a method for creating a base coordinate system for the installation of a collaborative production line of a numerical control equipment group. This method takes the numerical control equipment group collaborative system production line 1 as an application scenario as an embodiment, and creates a base coordinate system for different types of production lines. Compared with the existing method of creating the base coordinate system 5 with the reference numerical control equipment 4 as a reference, the digital adjustment of the 2 poses of the numerical control equipment with the number of axes avoids the situation that the equipment at the far end of the production line is installed outside the foundation embedded board .
[0036] The specific implementation process of the present invention is as follows figure 1 shown, including the following steps:
[0037] 1) use the level meter 8 to level the upper surface of ...
Embodiment 2
[0046] On the basis of Embodiment 1, in order to better realize the method of the present invention, refer to Figure 4 scene model and Figure 5 Geometric model, and further describe the step 1) in detail.
[0047] The specific method of fitting the reference plane 11 of the production line is as follows: the spatial position measuring instrument 6 measures the coordinates h (x i ,y i ,z i ), simplify the general formula plane equation (1) to formula (2), and then convert it to the equation of formula (3), and use the plane to fit the least squares model, that is, to obtain the smallest variance of the distances from all points to the plane, use The multiple linear regression least squares estimation model (5) and the optimal solution matrix algorithm (6) are used to solve the optimal general plane equation parameters b(a 0 , a 1 , a 2 ), and then obtain the equation of the reference plane P of the production line.
[0048] Ax+By+Cz+D=0 Formula (1)
[0049]
[0050...
PUM
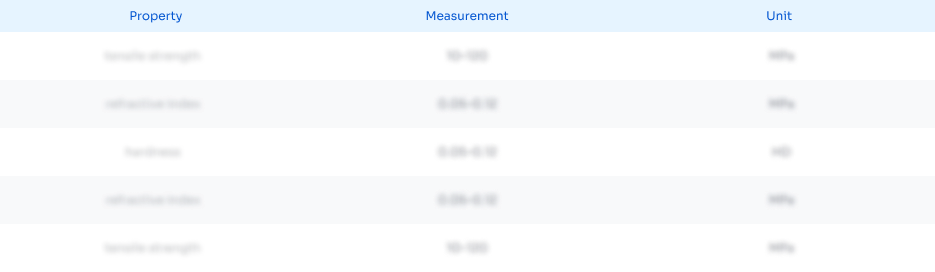
Abstract
Description
Claims
Application Information

- R&D
- Intellectual Property
- Life Sciences
- Materials
- Tech Scout
- Unparalleled Data Quality
- Higher Quality Content
- 60% Fewer Hallucinations
Browse by: Latest US Patents, China's latest patents, Technical Efficacy Thesaurus, Application Domain, Technology Topic, Popular Technical Reports.
© 2025 PatSnap. All rights reserved.Legal|Privacy policy|Modern Slavery Act Transparency Statement|Sitemap|About US| Contact US: help@patsnap.com