Weldable aluminum alloy comprising Zn as main alloying element for direct metal laser sintering
An aluminum alloy and laser diffraction technology, which is applied in metal processing equipment, transportation and packaging, and improvement of process efficiency, can solve problems such as limited shape combinations and inability to build parts with aluminum alloys
- Summary
- Abstract
- Description
- Claims
- Application Information
AI Technical Summary
Problems solved by technology
Method used
Image
Examples
example 1
[0069] For the following samples 1 and 2, the Al7017 alloy type composite was composed of Al7017 pre-alloyed (d50=38 μm), Zr powder (d50=30 μm) and B 4 The powder of C powder (d50=13μm) or TiC nano powder (d50<40nm) is dry-blended. Al7017 has the following composition: 0.42 wt.-% Si, 0.5 wt.-% Fe, 0.11 wt.-% Cu, 0.27 wt.-% Mn, 2.8 wt.-% Mg, 4.7 wt.-% Zn and 0.23 wt.-% Zr.
[0070] For samples 3 and 4, in addition to Zr and TiC additives, a dry powder mixture of Al7017 pre-alloyed (d50 = 48 μm) was used with a composition of 0.44 wt.-% Si, 0.43 wt.-% Fe, <0.01 wt. -% Cu, 0.24 wt.-% Mn, 2.5 wt.-% Mg, 4.6 wt.-% Zn and 0.2 wt.-% Zr. In these samples, the respective additives were Zr powder (d50=30 μm) and TiC powder (d50=1.4 μm). All respective raw materials were obtained from commercial powder producers. The ingredients of the powder mix are provided in Table I below.
[0071] Table I. Composition of Powder Mixtures
[0072]
[0073]
[0074] The powder mixes were prepa...
example 2
[0088] By dry mixing Al7075 pre-alloyed (d50=48μm) powder, Zr powder (d50=30μm) and B 4 C powder (d50=13 μm) to make Al7075 alloy type composites. Al7075 has the following composition: 0.08wt.-% Si, 0.17wt.-% Fe, 0.22wt.-% Cr, 1.7wt.-% Cu, 0.008wt.-% Mn, 2.0wt.-% Mg, 5.3 wt.-% Zn and 0.004 wt.-% Zr. The respective raw materials were obtained from commercial powder producers. The ingredients of the powder mix are provided in Table III below.
[0089] Table III. Composition of Powder Mixtures
[0090] Sample 5 Al alloy powder remaining Zr 4.0 B 4 C
0.8
[0091] The powder mix was prepared by mechanical dry blending the ingredients using a commercially available Merris SpinMix 550 mixer for 90 min at a speed of about 20 rpm.
[0092] The compositions described in Table III were processed into 3D objects by DMLS on an EOS M290 machine. Appropriate DMLS processing parameters were determined by screening experiments involving the fabricati...
PUM
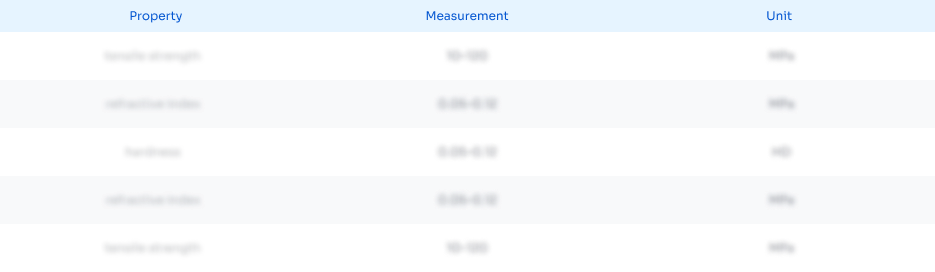
Abstract
Description
Claims
Application Information

- R&D Engineer
- R&D Manager
- IP Professional
- Industry Leading Data Capabilities
- Powerful AI technology
- Patent DNA Extraction
Browse by: Latest US Patents, China's latest patents, Technical Efficacy Thesaurus, Application Domain, Technology Topic, Popular Technical Reports.
© 2024 PatSnap. All rights reserved.Legal|Privacy policy|Modern Slavery Act Transparency Statement|Sitemap|About US| Contact US: help@patsnap.com