Ultrahigh-pressure long-life throttle valve for testing high-pressure pump for petroleum drilling
An oil drilling and ultra-high pressure technology is applied in the field of ultra-high pressure and long-life throttle valves for oil drilling high-pressure pump testing. , The effect of reducing maintenance costs and prolonging service life
- Summary
- Abstract
- Description
- Claims
- Application Information
AI Technical Summary
Problems solved by technology
Method used
Image
Examples
Embodiment Construction
[0032] The present invention can be explained in detail through the following examples, and the purpose of disclosing the present invention is to protect all technical improvements within the scope of the present invention.
[0033] An ultra-high pressure long-life throttle valve for oil drilling high-pressure pump testing, comprising a valve body assembly 1 and a valve core assembly 2; the valve body assembly 1 includes a valve body 1.1, a valve cover 1.2, an upper valve sleeve 1.3, a valve seat 1.4, an outlet Valve seat 1.5; valve body 1.1 is provided with upper valve sleeve hole 1.1.1, valve body cavity 1.1.2, valve seat hole 1.1.4, valve body outlet hole 1.1.5, valve body cavity 1.1. 2 The side wall is provided with an inclined water inlet 1.1.3; the valve cover 1.2 is fixed on the upper end of the valve body 1.1; the upper valve sleeve 1.3 is fixed in the upper valve sleeve hole 1.1.1, the upper end of the upper valve sleeve 1.3 and the valve cover 1.2 The lower end is in...
PUM
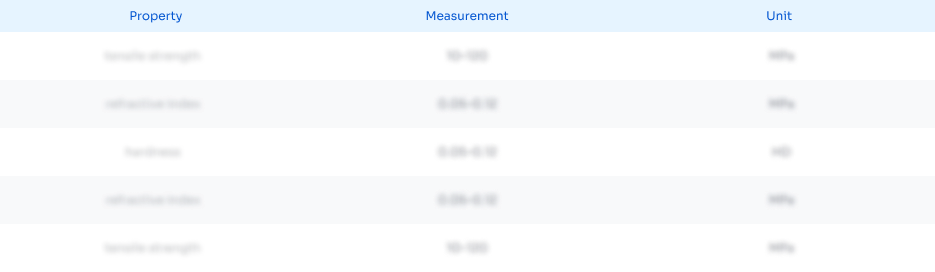
Abstract
Description
Claims
Application Information

- R&D
- Intellectual Property
- Life Sciences
- Materials
- Tech Scout
- Unparalleled Data Quality
- Higher Quality Content
- 60% Fewer Hallucinations
Browse by: Latest US Patents, China's latest patents, Technical Efficacy Thesaurus, Application Domain, Technology Topic, Popular Technical Reports.
© 2025 PatSnap. All rights reserved.Legal|Privacy policy|Modern Slavery Act Transparency Statement|Sitemap|About US| Contact US: help@patsnap.com