Pneumatic vibration device with rotatable piston shaft
A pneumatic vibration, piston shaft technology, applied in the direction of the drive device, fluid using vibration, boring machine/drilling machine components, etc., can solve the problems of easy wear of friction pairs, difficult manufacturing, high material requirements, etc., to improve chip removal ability and reduce Effect of cutting resistance, cutting temperature, and surface quality improvement
- Summary
- Abstract
- Description
- Claims
- Application Information
AI Technical Summary
Problems solved by technology
Method used
Image
Examples
Embodiment 2
[0060] like Figure 7As shown, on the basis of Embodiment 1, there is no first exhaust groove 206 in this embodiment. In this way, when the mechanism is working, with the rotation of the ventilation shaft 201 of the gas commutator 2, the first exhaust groove 206 will The pressure in the piston chamber 120 is periodically increased without pressure relief, while the second piston chamber 122 is periodically pressurized and depressurized; such a design will result in a larger downward impact force when the piston shaft A1 vibrates, The upward impact is weaker.
[0061] Further, the gas commutator 2 may be electromagnetic, and its function is to supply the external pressure gas to the first piston cavity and the second piston cavity of the piston body alternately at a certain frequency. The structure of the electromagnetic gas commutator is not limited, and its exchange frequency can be adjusted.
Embodiment 3
[0063] like Figure 8 As shown, on the basis of Embodiment 1, in this embodiment, the first piston 106 and the second piston 107 may also include a diaphragm structure, for example, an annular groove 106-3 is opened on the side of the first piston 106, An elastic diaphragm 106-4 is embedded in the annular groove 106-3, and the elastic diaphragm 106-4 has the function of supporting and sealing. When the piston shaft A1 vibrates, the elastic diaphragm 106-4 can deform. The same is true for the second piston 107 .
[0064] Such a design is effective for vibrations with small amplitudes, and at the same time, the machining difficulty of the piston is greatly reduced. Further, the elastic diaphragm 106-4 may be made of polymer material or metal material, and its structure and installation method are not limited.
PUM
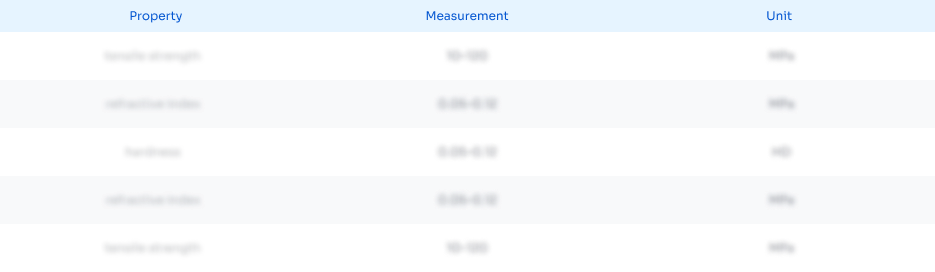
Abstract
Description
Claims
Application Information

- Generate Ideas
- Intellectual Property
- Life Sciences
- Materials
- Tech Scout
- Unparalleled Data Quality
- Higher Quality Content
- 60% Fewer Hallucinations
Browse by: Latest US Patents, China's latest patents, Technical Efficacy Thesaurus, Application Domain, Technology Topic, Popular Technical Reports.
© 2025 PatSnap. All rights reserved.Legal|Privacy policy|Modern Slavery Act Transparency Statement|Sitemap|About US| Contact US: help@patsnap.com