Preparation method of hydrotalcite-based CoNiV composite oxide catalyst and escape ammonia removal application
A composite oxide, hydrotalcite-based technology, applied in metal/metal oxide/metal hydroxide catalysts, physical/chemical process catalysts, chemical instruments and methods, etc., can solve problems such as low temperature activity to be improved
- Summary
- Abstract
- Description
- Claims
- Application Information
AI Technical Summary
Problems solved by technology
Method used
Image
Examples
Embodiment 1
[0043] Example 1: c(Co 2+ ):c(Ni 2+ ):c(V 3+ ) =1:2:1
[0044] (1) Weigh 2.379 g of cobalt chloride hexahydrate, 1.573 g of vanadium chloride, and 4.753 g of nickel chloride hexahydrate into a beaker, add 100 ml of deionized water, and stir with a magnetic stirrer for 20 min to dissolve them completely. use;
[0045] (2) Add 10.82 g of urea to the mixed salt solution prepared above to dissolve it and stir evenly.
[0046] (3) Continue to stir the mixed solution obtained in (2) for 30 min with a magnetic stirrer, and measure the pH value of the mixed solution with a pH meter.
[0047] (4) Then the obtained mixed solution was sealed and placed in a polytetrafluoroethylene-lined stainless steel reactor, and hydrothermally treated in an oven at 110±2 °C for 12 h.
[0048] (5) After the reaction kettle is naturally cooled, filter the reacted solution to get the precipitate, wash it with deionized water several times until neutral, put it in an oven to dry at 60±2°C for 12 hour...
Embodiment 2
[0051] Example 2: c(Co 2+ ):c(Ni 2+ ):c(V 3+ ) =1.5:1.5:1
[0052] (1) Weigh 3.569 g of cobalt chloride hexahydrate, 1.573 g of vanadium chloride, and 3.565 g of nickel chloride hexahydrate into a beaker, add 100 ml of deionized water, and stir with a magnetic stirrer for 20 min to dissolve completely. use;
[0053] (2) Add 10.82 g of urea to the mixed salt solution prepared above to dissolve it and stir evenly.
[0054] (3) Continue to stir the mixed solution obtained in (2) for 30 min with a magnetic stirrer, and measure the pH value of the mixed solution with a pH meter.
[0055] (4) Then the obtained mixed solution was sealed and placed in a polytetrafluoroethylene-lined stainless steel reactor, and hydrothermally treated in an oven at 110±2 °C for 12 h.
[0056] (5) After the reaction kettle is naturally cooled, filter the reacted solution to get the precipitate, wash it with deionized water several times until neutral, put it in an oven to dry at 60±2°C for 12 hours...
Embodiment 3
[0059] Example 3: c(Co 2+ ):c(Ni 2+ ):c(V 3+ ) =2:1:1
[0060] (1) Weigh 4.759 g of cobalt chloride hexahydrate, 1.573 g of vanadium chloride, and 2.377 g of nickel chloride hexahydrate into a beaker, add 100ml of deionized water, and stir with a magnetic stirrer for 20 minutes to dissolve completely, and set aside ;
[0061] (2) Add 10.82 g of urea to the mixed salt solution prepared above to dissolve it and stir evenly.
[0062] (3) Continue to stir the mixed solution obtained in (2) for 30 min with a magnetic stirrer, and measure the pH value of the mixed solution with a pH meter.
[0063] (4) Then the obtained mixed solution was sealed and placed in a polytetrafluoroethylene-lined stainless steel reactor, and hydrothermally treated in an oven at 110±2 °C for 12 h.
[0064] (5) After the reaction kettle is naturally cooled, filter the reacted solution to get the precipitate, wash it with deionized water several times until neutral, put it in an oven to dry at 60±2°C fo...
PUM
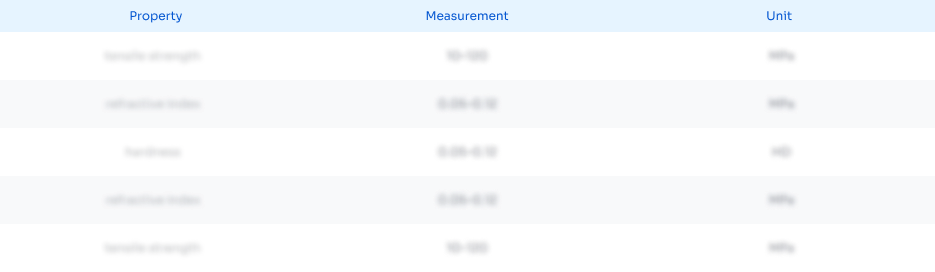
Abstract
Description
Claims
Application Information

- R&D
- Intellectual Property
- Life Sciences
- Materials
- Tech Scout
- Unparalleled Data Quality
- Higher Quality Content
- 60% Fewer Hallucinations
Browse by: Latest US Patents, China's latest patents, Technical Efficacy Thesaurus, Application Domain, Technology Topic, Popular Technical Reports.
© 2025 PatSnap. All rights reserved.Legal|Privacy policy|Modern Slavery Act Transparency Statement|Sitemap|About US| Contact US: help@patsnap.com