Preforming process of rubber sheet for vulcanization of shock insulation support
A technology of pre-forming and vibration-isolating rubber, applied in the field of vibration-isolating rubber products, can solve the problems of shortening the pre-forming time of the film of the vibration-isolating rubber bearing, bonding of isolation pads, etc., and achieve automatic reverse opening and fixed-length cutting. , Reduce the degree of adhesion, avoid the effect of pulling and curling deformation
- Summary
- Abstract
- Description
- Claims
- Application Information
AI Technical Summary
Problems solved by technology
Method used
Examples
Embodiment 1
[0024] Example 1: After the mixed rubber is discharged from the internal mixer, it is first unloaded through an open mill. The thickness of the film is adjusted by the roll distance of the open mill, and the width of the film is adjusted by the distance between the baffles of the open mill, so as to be continuous and smooth. The form of the film is neatly stored on the plastic tray, and then sent to the cold feed extruder through the automatic glue supply conveyor belt. After calendering, the film is pressed out for thickness and width monitoring, and then forced air cooling in the form of continuous flat belt transmission. After cooling, the temperature of the film is controlled at 45±10°C, and then sliced by an intelligent digital vibration cutting system. Finally, the film is weighed and processed. According to the weight of each vibration-isolating rubber bearing, the glue is collected and stacked on the louver. The cut film is isolated with 0.1mm PTFE soft board. The num...
Embodiment 2
[0025]Example 2: After the mixed rubber is discharged from the internal mixer, it is first unloaded through an extruder. The thickness and width of the film are adjusted by the size of the extrusion die, and it is neatly stored in the plastic in the form of a continuous and smooth film. On the tray, it is then sent to the cold feed extruder through the automatic glue supply conveyor belt. After extrusion, the temperature is controlled at 90±10℃, and the automatic continuous glue supply conveyor belt enters the four-roll calender for calendering. The film is extruded for thickness and After the width is monitored, forced air cooling is carried out in the form of continuous rollers. After cooling, the temperature of the film is controlled at 40±10°C, and then sliced by an intelligent digital vibration cutting system. The weight of the glue is collected and stacked on the louver. The cut film is isolated with a 0.1mm PTFE soft board. The number of layers of film on each louver i...
Embodiment 3
[0026] Example 3: After the mixed rubber is discharged from the internal mixer, it is first unloaded through an extruder. The thickness and width of the film are adjusted by the size of the extrusion die, and it is neatly stored in the plastic in the form of a continuous and smooth film. On the tray, it is then sent to the cold feed extruder through the automatic glue supply conveyor belt. After extrusion, the temperature is controlled at 90±10℃, and the automatic continuous glue supply conveyor belt enters the four-roll calender for calendering. The film is extruded for thickness and After the width is monitored, forced air cooling is carried out in the form of continuous rollers. Cooling water is connected to the inside of the rollers. After cooling, the temperature of the film is controlled at 30±10°C, and then sliced by an intelligent digital vibration cutting system. The glued weight of each shock-isolating rubber bearing is collected and stacked on the louver. The cut f...
PUM
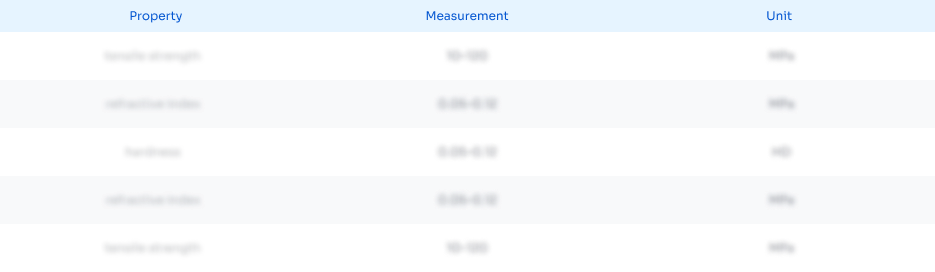
Abstract
Description
Claims
Application Information

- R&D Engineer
- R&D Manager
- IP Professional
- Industry Leading Data Capabilities
- Powerful AI technology
- Patent DNA Extraction
Browse by: Latest US Patents, China's latest patents, Technical Efficacy Thesaurus, Application Domain, Technology Topic, Popular Technical Reports.
© 2024 PatSnap. All rights reserved.Legal|Privacy policy|Modern Slavery Act Transparency Statement|Sitemap|About US| Contact US: help@patsnap.com