Electric drive integrated NVH simulation modeling method
A simulation modeling, electric drive technology, applied in design optimization/simulation, 3D modeling, multi-objective optimization, etc., can solve problems such as inaccurate results, low simulation efficiency, and inability to consider the coupling effect of the motor and the reducer. The effect of reducing the amount of calculation, ensuring accuracy, and saving manual setup and analysis time
- Summary
- Abstract
- Description
- Claims
- Application Information
AI Technical Summary
Problems solved by technology
Method used
Image
Examples
Embodiment 1
[0045] This embodiment provides an electric drive integrated NVH simulation modeling method, refer to the process figure 1 This embodiment can be better understood, and the specific method includes the following steps:
[0046] Step 1. Carry out detailed finite element modeling of the components of the electric drive system;
[0047] Step 2. Use the elastic element to constrain the suspension bracket, set the elastic modulus of the elastic element in the three directions of X-axis, Y-axis and Z-axis according to the actual suspension stiffness parameters, assemble the established finite element model, and establish the electric drive Assembly structure finite element model;
[0048] Step 3. Simplify the finite element model of the electric drive assembly structure and coarsen the mesh size of the model;
[0049] Step 4. Correct the size of the coarsened grid to obtain a coarsened grid with suitable precision;
[0050] Step 5. Envelope the electric drive model with a coarse me...
Embodiment 2
[0055] This embodiment is a further limitation of Embodiment 1. The components of the electric drive system described in step 1 include a motor, a reducer, an inverter, and a suspension bracket.
Embodiment 3
[0057] This embodiment is a further limitation of Embodiment 2. The motor includes a stator, a rotor and a casing of the motor, the reducer includes a reducer casing and a gear reducer shaft tooth structure, and the inverter includes an inverter shell and its internal structure.
[0058] In this embodiment, finite element models are established for each component of the electric drive system, including all shells and internal structures of all electric drive systems, so as to ensure high accuracy of subsequent simulation calculation results.
PUM
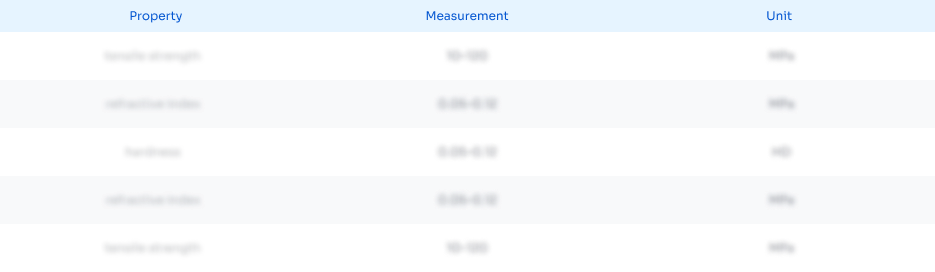
Abstract
Description
Claims
Application Information

- R&D
- Intellectual Property
- Life Sciences
- Materials
- Tech Scout
- Unparalleled Data Quality
- Higher Quality Content
- 60% Fewer Hallucinations
Browse by: Latest US Patents, China's latest patents, Technical Efficacy Thesaurus, Application Domain, Technology Topic, Popular Technical Reports.
© 2025 PatSnap. All rights reserved.Legal|Privacy policy|Modern Slavery Act Transparency Statement|Sitemap|About US| Contact US: help@patsnap.com