Implementation method of automatic compensation for thermal deformation of machine tool
A technology of automatic compensation and realization method, applied in automatic control devices, metal processing mechanical parts, metal processing and other directions, can solve the problems of incompatibility, long development cycle, low thermal compensation accuracy, etc., to reduce development costs and shorten development cycles. , the effect of high compensation accuracy
- Summary
- Abstract
- Description
- Claims
- Application Information
AI Technical Summary
Problems solved by technology
Method used
Image
Examples
Embodiment 1
[0038] A method for realizing automatic compensation of thermal deformation of a machine tool adopts an advanced technical scheme based on the combination of a thermal imager, a high-precision position measuring instrument, a temperature measuring instrument and finite element analysis technology. The implementation process is divided into: establishment of the finite element model of the machine tool; detection of the actual temperature field and thermal deformation of the machine tool; correction of the finite element model of the temperature field and thermal deformation of the machine tool; finite element virtual analysis of the thermal compensation of the machine tool; development of the thermal compensation control device and its actual effect Verification and other 5 stages. It includes the following steps:
[0039] 1) Establish a three-dimensional CAD model of the machine tool;
[0040] 2) Measure the temperature field of the machine tool;
[0041] 3) Establish a fin...
Embodiment 2
[0049] On the basis of Embodiment 1, the establishment of the three-dimensional CAD model of the machine tool is based on the design drawing of the machine tool parts, using three-dimensional design software such as Solidedge, to establish the three-dimensional CAD part models of the various parts of the machine tool, and assemble them into the overall CAD of the machine tool parts model, and then assemble the overall CAD model of each component into the overall CAD model of the machine tool. The actual measurement of the temperature field of the machine tool is to use the thermal imager to test the machine base, bed, column, The temperature field distribution map of the headstock, spindle and other components, and save it in JPG (or other) graphic file format. The establishment of the finite element model of the thermal characteristics of the machine tool is through the interface of the 3D modeling software such as Solidedge and the finite element analysis software such as AN...
PUM
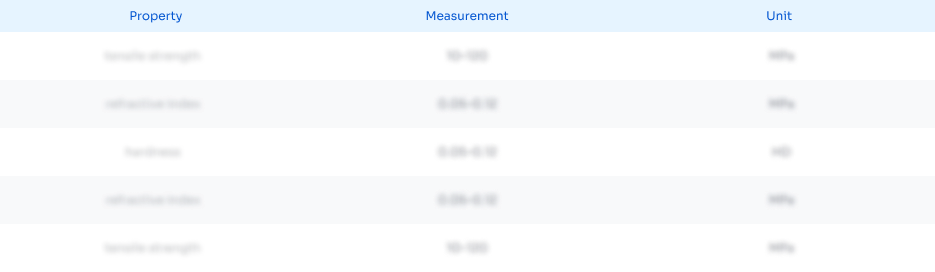
Abstract
Description
Claims
Application Information

- R&D
- Intellectual Property
- Life Sciences
- Materials
- Tech Scout
- Unparalleled Data Quality
- Higher Quality Content
- 60% Fewer Hallucinations
Browse by: Latest US Patents, China's latest patents, Technical Efficacy Thesaurus, Application Domain, Technology Topic, Popular Technical Reports.
© 2025 PatSnap. All rights reserved.Legal|Privacy policy|Modern Slavery Act Transparency Statement|Sitemap|About US| Contact US: help@patsnap.com