Alkali-activated composite recycled powder recycled aggregate pervious concrete and preparation method thereof
A technology of permeable concrete and recycled aggregate, applied in the field of building materials, can solve the problems of high production cost, insufficient digestion of construction waste, unused and other problems
- Summary
- Abstract
- Description
- Claims
- Application Information
AI Technical Summary
Problems solved by technology
Method used
Image
Examples
Embodiment 1
[0034] 1) Weigh 6 parts of fly ash, 15 parts of mineral powder, 6 parts of brick powder, 8 parts of water, 30 parts of single particle size aggregate, 15 parts of recycled aggregate in saturated surface dry state, and 4 parts of alkaline activator according to the proportion of the formula. copy, spare;
[0035] 2) Add single-size aggregate, recycled aggregate and 20% water in total to the mixer, stir for 40 seconds, then add mineral powder, fly ash, brick powder and the remaining water in sequence, and continue stirring for 2 minutes; Finally, add the alkaline activator and continue to stir for 2 minutes to form porous concrete;
[0036] 3) the porous concrete obtained in step 2) is divided into two times and packed into a mould, vibrated and formed;
[0037] 4) After forming, the surface of the test piece with mold is covered with plastic film, and the mold is removed within 24 hours;
[0038] 5) After demoulding, heat preservation, moisture retention and maintenance shall...
Embodiment 2
[0040] 1) Weigh 11 parts of fly ash, 12 parts of mineral powder, 4 parts of brick powder, 5 parts of water, 50 parts of single-size aggregate, 30 parts of recycled aggregate in saturated surface dry state, and 6 parts of alkaline activator according to the proportion of the formula. copy, spare;
[0041] 2) Add single particle size aggregate, recycled aggregate and water with a total water content of 25% into the mixer, stir for 30 seconds, then add mineral powder, fly ash, brick powder and the remaining water in sequence, and continue stirring for 1.5 minutes; Finally, add the alkaline activator and continue to stir for 3 minutes to form porous concrete;
[0042] 3) the porous concrete obtained in step 2) is divided into two times and packed into a mould, vibrated and formed;
[0043] 4) After forming, the surface of the test piece with mold is covered with plastic film, and the mold is removed within 24 hours;
[0044] 5) After demoulding, heat preservation, moisture reten...
Embodiment 3
[0046] 1) Weigh 16 parts of fly ash, 5 parts of mineral powder, 2 parts of brick powder, 2 parts of water, 40 parts of single particle size aggregate, 10 parts of recycled aggregate in saturated surface dry state, and 5 parts of alkaline activator according to the formula ratio. copy, spare;
[0047] 2) Add single-size aggregate, recycled aggregate and 30% water in total to the mixer, stir for 20 seconds, then add mineral powder, fly ash, brick powder and the remaining water in sequence, and continue stirring for 1 minute; Finally, add the alkaline activator and continue to stir for 1 minute to form porous concrete;
[0048] 3) the porous concrete obtained in step 2) is divided into two times and packed into a mould, vibrated and formed;
[0049] 4) After forming, the surface of the test piece with mold is covered with plastic film, and the mold is removed within 24 hours;
[0050] 5) After demoulding, heat preservation, moisture retention and maintenance shall not be less tha...
PUM
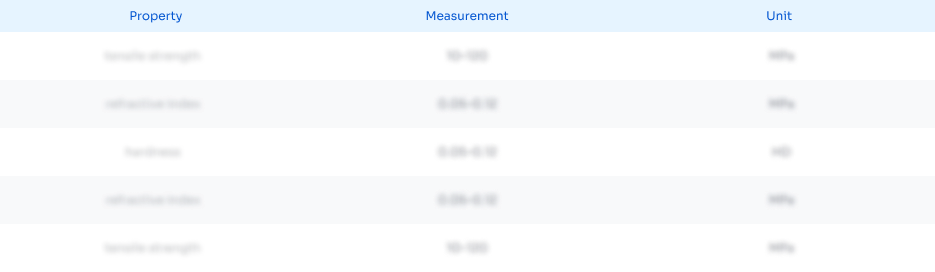
Abstract
Description
Claims
Application Information

- R&D Engineer
- R&D Manager
- IP Professional
- Industry Leading Data Capabilities
- Powerful AI technology
- Patent DNA Extraction
Browse by: Latest US Patents, China's latest patents, Technical Efficacy Thesaurus, Application Domain, Technology Topic, Popular Technical Reports.
© 2024 PatSnap. All rights reserved.Legal|Privacy policy|Modern Slavery Act Transparency Statement|Sitemap|About US| Contact US: help@patsnap.com