Sheet molding compound and preparation method thereof
A technology of sheet molding compound and release agent, which is applied in the field of sheet molding compound and its preparation, can solve the problems of not meeting the requirements of mechanical properties and insulation properties, the value of finished products is not proportional, and the cost of carbon fiber is high, so as to achieve good mechanical properties , Good molding effect, high compressive strength
- Summary
- Abstract
- Description
- Claims
- Application Information
AI Technical Summary
Problems solved by technology
Method used
Image
Examples
preparation example Construction
[0040] Preparation example of basalt fiber
[0041] The basalt fiber in the following raw materials was purchased from the chopped basalt fiber produced by Tai’an Haosong Fiber Co., Ltd., with a length of 3 mm; other raw materials and equipment are commercially available.
preparation example 1
[0042] Preparation example 1: Basalt fiber is prepared by the following method:
[0043] ⅠWeigh the basalt fiber and place it in 10% sodium hydroxide aqueous solution for soaking, grind it for 2.5min at a speed of 110r / min during soaking, then take out the basalt fiber and place it in 5% sodium lauroyl sarcosinate Soak and stir in the aqueous solution, stir for 2 minutes at a rotating speed of 80r / min, then take out the basalt fiber to obtain a semi-finished product;
[0044] Ⅱ Weigh rosin and place it in absolute ethanol, stir at 70°C until it is completely dissolved, and obtain a rosin ethanol solution with a mass fraction of 10%, weigh 2 kg of rosin ethanol solution and spray evenly on the surface of 10 kg of semi-finished products, and after drying, obtain Modified basalt fiber.
preparation example 2
[0045] Preparation example 2: Basalt fiber is prepared by the following method:
[0046] ⅠWeigh the basalt fiber and place it in 5% sodium hydroxide aqueous solution by mass fraction for soaking, grind it for 5 minutes at a rotating speed of 80r / min during the soaking process, then take out the basalt fiber and place it in 2% mass fraction of sodium lauroyl sarcosinate aqueous solution Soak and stir in medium, stir 3min under the rotating speed of 80r / min, then take out basalt fiber, make semi-finished product;
[0047] Ⅱ Weigh rosin and place it in absolute ethanol, stir at 70°C until completely dissolved to obtain a rosin ethanol solution with a mass fraction of 5%, weigh 1 kg of rosin ethanol solution and spray evenly on the surface of 10 kg of semi-finished products, and after drying, obtain Modified basalt fiber.
PUM
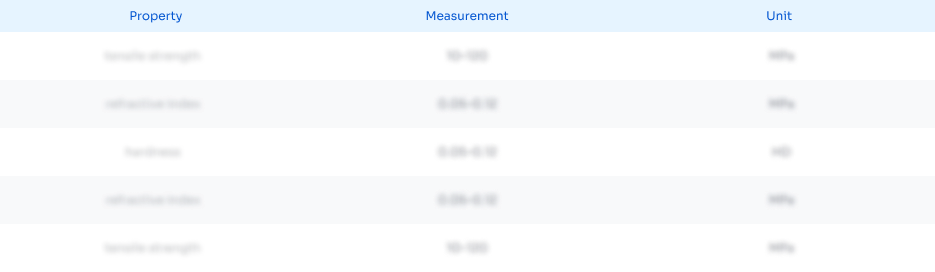
Abstract
Description
Claims
Application Information

- R&D
- Intellectual Property
- Life Sciences
- Materials
- Tech Scout
- Unparalleled Data Quality
- Higher Quality Content
- 60% Fewer Hallucinations
Browse by: Latest US Patents, China's latest patents, Technical Efficacy Thesaurus, Application Domain, Technology Topic, Popular Technical Reports.
© 2025 PatSnap. All rights reserved.Legal|Privacy policy|Modern Slavery Act Transparency Statement|Sitemap|About US| Contact US: help@patsnap.com