Method for eliminating residual stress of magnesium alloy deformed processing material
A technology of deformation processing and residual stress, which is applied in the field of non-ferrous metal material processing, can solve the problems of alloy deformation failure, slow cooling speed, oversize, etc., and achieve the effect of excellent mechanical properties, high forming quality and elimination of residual stress
- Summary
- Abstract
- Description
- Claims
- Application Information
AI Technical Summary
Problems solved by technology
Method used
Examples
Embodiment 1
[0022] The cross-sectional area is 2.8×10 5 mm 2 The composition ratio of the magnesium alloy processing material is: Mg-8Gd-4Y-1Zr-0.5Mn (wt.%), and the post-deformation treatment method comprises the following steps:
[0023] (1) On-line quenching measures are taken during the extrusion process: use 87°C hot water at 5 cm from the exit of the extruder for primary water cooling quenching, after the primary quenching, use 20°C room temperature water at 27 cm from the exit of the extruder for secondary Level water cooling quenching, after the second level quenching, use the automatic blast system to blow cold air to carry out the third level air cooling quenching;
[0024] (2) Carry out simple pressure straightening treatment on the part with larger warpage in the extruded processed material;
[0025] (3) Put the deformed material into the furnace for cold treatment, the temperature is -150°C, and the holding time is 4 hours. At the same time, the electric pulse generator is ...
Embodiment 2
[0030] The cross-sectional area is 1.5×10 5 mm 2 The composition ratio of the magnesium alloy processing material is: Mg-9Y-1MM-1Zn-0.5Zr (wt.%), and the post-deformation treatment method comprises the following steps:
[0031] (1) On-line quenching measures are taken during the extrusion process: use 90°C hot water at 10cm from the exit of the extruder for primary water-cooling quenching, after the primary quenching, use 30°C room temperature water at 25cm from the exit of the extruder Level water cooling quenching, after the second level quenching, use the automatic blast system to blow cold air to carry out the third level air cooling quenching;
[0032] (2) Carry out simple pressure straightening treatment on the part with larger warpage in the extruded processed material;
[0033] (3) Put the deformed material into the furnace for cold treatment, the temperature is -50°C, and the holding time is 8 hours. At the same time, the electric pulse generator is connected, and t...
Embodiment 3
[0038] The cross-sectional area is 2.5×10 5 mm 2 The composition ratio of the magnesium alloy processing material is: Mg-6Gd-4Y-1Zr-1Zn (wt.%), and the post-deformation treatment method comprises the following steps:
[0039] (1) On-line quenching measures are taken during the extrusion process: use 86°C hot water for primary water cooling quenching at 8 cm from the exit of the extruder. Level water cooling quenching, after the second level quenching, use the automatic blast system to blow cold air to carry out the third level air cooling quenching;
[0040] (2) Carry out simple pressure straightening treatment on the part with larger warpage in the extruded processed material;
[0041] (3) Put the deformed material into the furnace for cold treatment, the temperature is -75°C, and the holding time is 4.5 hours. At the same time, the electric pulse generator is connected, and the electric pulse energy field is applied to assist the heat treatment. The pulse form is positive ...
PUM
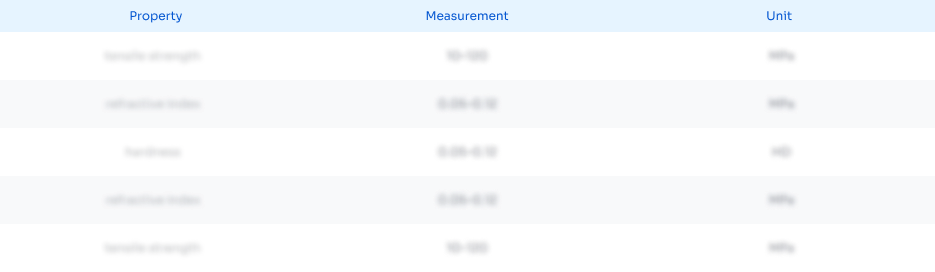
Abstract
Description
Claims
Application Information

- R&D
- Intellectual Property
- Life Sciences
- Materials
- Tech Scout
- Unparalleled Data Quality
- Higher Quality Content
- 60% Fewer Hallucinations
Browse by: Latest US Patents, China's latest patents, Technical Efficacy Thesaurus, Application Domain, Technology Topic, Popular Technical Reports.
© 2025 PatSnap. All rights reserved.Legal|Privacy policy|Modern Slavery Act Transparency Statement|Sitemap|About US| Contact US: help@patsnap.com