Partial premixed combustion device and method of oxygen-enriched combustion internal heating type coal low-temperature dry distillation furnace
A technology of oxygen-enriched combustion and premixed combustion, which is applied in the direction of combustion methods, special forms of dry distillation, burners, etc., and can solve problems such as uneven temperature distribution of the furnace section, unstable quality of dry distillation products, overheating of burners and fire channels, etc. , to achieve high value-added utilization, reduce hot spot temperature, and increase calorific value
- Summary
- Abstract
- Description
- Claims
- Application Information
AI Technical Summary
Problems solved by technology
Method used
Image
Examples
Embodiment 1
[0042] Example 1 is applied to an oxygen-enriched combustion internal heating coal low-temperature carbonization furnace with an oxygen enrichment rate of 83% and an annual output of 75,000 tons
[0043] (1) Basic information
[0044] A coal low-temperature carbonization furnace with an annual output of 75,000 tons of semi-coal has been built. Oxygen-enriched air with an oxygen-enriched rate of 83% is used to burn coal gas in the furnace to generate high-temperature heat carrier gas, which enters the furnace to provide heat for low-temperature coal carbonization. A total of 48 gas supply branches are arranged on both sides of the lower part of the furnace body to supply oxygen-enriched air and gas to the 48 fire channels respectively. Relevant facilities are fully equipped, including dry distillation furnace body, combustion-supporting fan, gas fan, raw material preparation (crushing and screening system), feeding system, gas export system, coke discharge system, gas purificat...
Embodiment 2
[0049] Example 2 is applied to an oxygen-enriched combustion internal heating coal low-temperature carbonization furnace with an oxygen-enriched rate of 65% and an annual output of 75,000 tons
[0050] (1) Basic information
[0051] A coal low-temperature carbonization furnace with an annual output of 75,000 tons of semi-coal has been built. Oxygen-enriched air with an oxygen-enriched rate of 65% is used to burn coal gas in the furnace to generate high-temperature heat carrier gas, which enters the furnace to provide heat for low-temperature coal carbonization. A total of 48 gas supply branches are arranged on both sides of the lower part of the furnace body to supply oxygen-enriched air and gas to the 48 fire channels respectively. Relevant facilities are fully equipped, including dry distillation furnace body, combustion-supporting fan, gas fan, raw material preparation (crushing and screening system), feeding system, gas export system, coke discharge system, gas purificatio...
Embodiment 3
[0056] Example 3 is applied to an oxygen-enriched combustion internal heating coal low-temperature carbonization furnace with an oxygen-enriched rate of 100% and an annual output of 112,500 tons
[0057] (1) Basic information
[0058] A coal low-temperature carbonization furnace with an annual output of 112,500 tons of semi-coal has been built. Oxygen-enriched air with an oxygen-enriched rate of 100% is used to burn coal gas in the furnace to generate high-temperature heat carrier gas, which enters the furnace to provide heat for low-temperature coal carbonization. A total of 72 gas supply branches are arranged on both sides of the lower part of the furnace body, supplying oxygen-enriched air and coal gas to 72 fire channels respectively. Relevant facilities are fully equipped, including dry distillation furnace body, combustion-supporting fan, gas fan, raw material preparation (crushing and screening system), feeding system, gas export system, coke discharge system, gas purif...
PUM
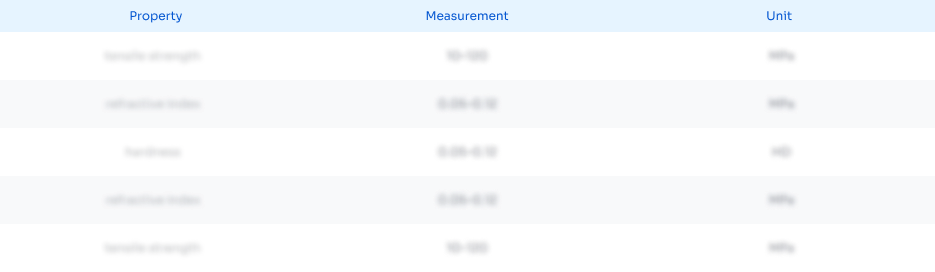
Abstract
Description
Claims
Application Information

- Generate Ideas
- Intellectual Property
- Life Sciences
- Materials
- Tech Scout
- Unparalleled Data Quality
- Higher Quality Content
- 60% Fewer Hallucinations
Browse by: Latest US Patents, China's latest patents, Technical Efficacy Thesaurus, Application Domain, Technology Topic, Popular Technical Reports.
© 2025 PatSnap. All rights reserved.Legal|Privacy policy|Modern Slavery Act Transparency Statement|Sitemap|About US| Contact US: help@patsnap.com