Glass fiber reinforced nylon 6 composite material
A glass fiber and composite material technology, applied in the field of glass fiber reinforced nylon 6 composite material, can solve the problems of low melt strength, poor tensile strength, low extrusion speed, etc.
- Summary
- Abstract
- Description
- Claims
- Application Information
AI Technical Summary
Problems solved by technology
Method used
Image
Examples
Embodiment 1
[0039] Glass fiber reinforced nylon 6 composite material, its preparation process comprises the steps:
[0040] Step 1: Weigh 48 parts of nylon 6, 20 parts of high-temperature nylon PPA, 5 parts of toughening agent POE-g-MAH, 0.3 parts of silane coupling agent, 0.2 parts of antioxidant, dispersion lubricant silicone master 0.5 parts of granules and 1 part of black masterbatch, first dry nylon 6 and high-temperature nylon PPA at 120°C for 4 hours, and then mix the remaining components with the dried nylon 6 and high-temperature nylon PPA in a high-speed mixer After 1-2 minutes, the premix is obtained;
[0041] Step 2: Add the premix prepared in Step 1 into the main feeding port of the twin-screw extruder (screw diameter: 60mm, length-to-diameter ratio L / D=48), glass fiber is added from the side feeding port, and the main engine is controlled The number of revolutions and the amount of feed ensure that the glass fiber content is controlled at 25%, and pelletized after being m...
Embodiment 2
[0044] Weigh 53 parts of nylon 6, 15 parts of high-temperature nylon PPA, 5 parts of POE-g-MAH, 0.3 part of silane coupling agent, 0.2 part of antioxidant, 0.5 part of dispersing lubricant silicone masterbatch and black masterbatch 1 part, first dry nylon 6 and high-temperature nylon PPA at 120°C for 4 hours, then put the remaining components and dried nylon 66 and high-temperature nylon PPA in a high-speed mixer and mix for 1 to 2 minutes to obtain For the premix, except that the glass fiber content is operated according to the above ratio, the rest of the steps are produced according to the step 2 process in the embodiment 1 to produce the heat insulation strip raw material and the step 3 operation to produce the heat insulation strip.
Embodiment 3
[0046] Weigh 60 parts of nylon 6, 10 parts of high-temperature nylon PPA, 3 parts of POE-g-MAH, 0.3 parts of silane coupling agent, 0.2 parts of antioxidant, 0.5 parts of silicone masterbatch of dispersion lubricant and black masterbatch 1 part, first dry nylon 6 and high-temperature nylon PPA at 120°C for 4 hours, then put the remaining components and dried nylon 6 and high-temperature nylon PPA in a high-speed mixer and mix for 1 to 2 minutes to obtain For the premix, except that the glass fiber content is operated according to the above ratio, the rest of the steps are produced according to the step 2 process in the embodiment 1 to produce the heat insulation strip raw material and the step 3 operation to produce the heat insulation strip.
PUM
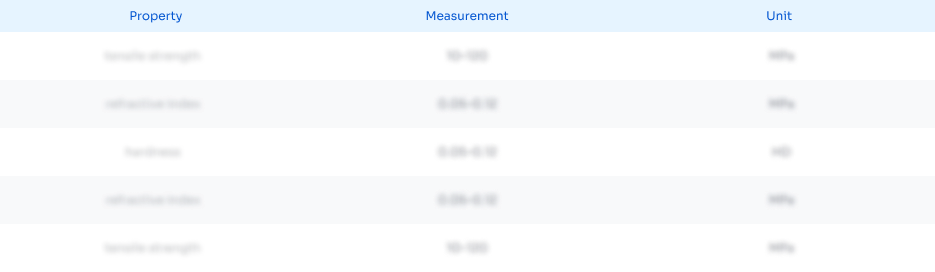
Abstract
Description
Claims
Application Information

- R&D
- Intellectual Property
- Life Sciences
- Materials
- Tech Scout
- Unparalleled Data Quality
- Higher Quality Content
- 60% Fewer Hallucinations
Browse by: Latest US Patents, China's latest patents, Technical Efficacy Thesaurus, Application Domain, Technology Topic, Popular Technical Reports.
© 2025 PatSnap. All rights reserved.Legal|Privacy policy|Modern Slavery Act Transparency Statement|Sitemap|About US| Contact US: help@patsnap.com