Special anti-radiation glass for nuclear power station and preparation process of special anti-radiation glass
A preparation process and radiation protection technology, applied in glass manufacturing equipment, glass pressing, manufacturing tools, etc., can solve the problems that the radiation protection layer cannot play a radiation protection effect, the glass does not have a radiation protection effect, and the price of radiation protection glass is high , to achieve a good protective effect, improve the anti-radiation effect, and improve the effect of environmental safety
- Summary
- Abstract
- Description
- Claims
- Application Information
AI Technical Summary
Problems solved by technology
Method used
Image
Examples
Embodiment 1
[0019] A special anti-radiation glass for nuclear power plants, the composition of raw materials is composed of the following proportions in parts by weight: 76 parts of silicon dioxide, 14 parts of lead oxide, 11 parts of titanium dioxide, 9 parts of barium oxide, 12 parts of aluminum oxide, 7 parts of magnesium oxide, 7 parts of methyl methacrylate, 13 parts of manganese oxide, 2 parts of iron oxide, 4 parts of potassium oxide, 3 parts of silver oxide, 24 parts of hydrofluoric acid, 32 parts of acetic acid, 28 parts of phenolic resin.
[0020] Preferably, its preparation process comprises the following steps:
[0021] A. In an atmospheric pressure environment, put an appropriate amount of silicon dioxide and a certain amount of phenolic resin into the reaction kettle according to the ratio of 5:1 for stirring, and add an appropriate amount of hydrofluoric acid to react, and the temperature is controlled at 24°C ;
[0022] B. Add a certain proportion of titanium dioxide and ...
Embodiment 2
[0028] A special anti-radiation glass for nuclear power plants. The raw materials are composed of the following proportions in parts by weight: 56 parts of silicon dioxide, 15 parts of lead oxide, 10 parts of titanium dioxide, 10 parts of barium oxide, 10 parts of aluminum oxide, 8 parts of magnesium oxide, 6 parts of methyl methacrylate, 15 parts of manganese oxide, 2 parts of iron oxide, 5 parts of potassium oxide, 2 parts of silver oxide, 25 parts of hydrofluoric acid, 23 parts of acetic acid, 30 parts of phenolic resin.
[0029] Preferably, its preparation process comprises the following steps:
[0030] A. Under an atmospheric pressure environment, put an appropriate amount of silicon dioxide and a certain amount of phenolic resin into the reaction kettle according to the ratio of 5:1 for stirring, and add an appropriate amount of hydrofluoric acid to react, and the temperature is controlled at 20°C ;
[0031] B. Add a certain proportion of titanium dioxide and potassium ...
Embodiment 3
[0037] A special anti-radiation glass for nuclear power plants. The raw materials are composed of the following proportions in parts by weight: 80 parts of silicon dioxide, 13 parts of lead oxide, 12 parts of titanium dioxide, 8 parts of barium oxide, 15 parts of aluminum oxide, 5 parts of magnesium oxide, 8 parts of methyl methacrylate, 12 parts of manganese oxide, 3 parts of iron oxide, 3 parts of potassium oxide, 3 parts of silver oxide, 20 parts of hydrofluoric acid, 35 parts of acetic acid, 10 parts of phenolic resin.
[0038] Preferably, its preparation process comprises the following steps:
[0039] A. Under an atmospheric pressure environment, put an appropriate amount of silicon dioxide and a certain amount of phenolic resin into the reaction kettle according to the ratio of 5:1 for stirring, and add an appropriate amount of hydrofluoric acid to react, and the temperature is controlled at 30°C ;
[0040] B. Add a certain proportion of titanium dioxide and potassium o...
PUM
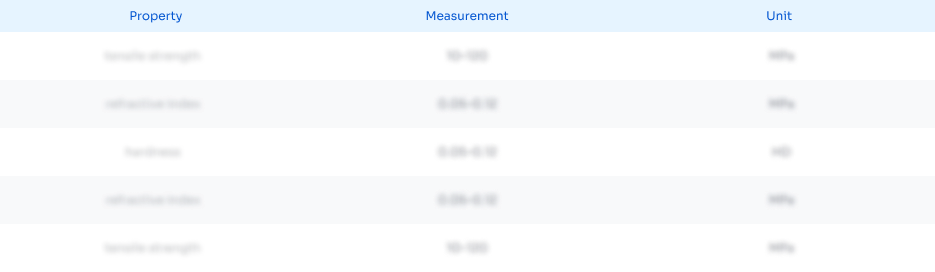
Abstract
Description
Claims
Application Information

- Generate Ideas
- Intellectual Property
- Life Sciences
- Materials
- Tech Scout
- Unparalleled Data Quality
- Higher Quality Content
- 60% Fewer Hallucinations
Browse by: Latest US Patents, China's latest patents, Technical Efficacy Thesaurus, Application Domain, Technology Topic, Popular Technical Reports.
© 2025 PatSnap. All rights reserved.Legal|Privacy policy|Modern Slavery Act Transparency Statement|Sitemap|About US| Contact US: help@patsnap.com