Bearing pad machining method
A processing method and pad technology, which are applied in the field of bearing pad processing and pad processing, can solve the problems of increased processing difficulty and difficulty in guaranteeing the dimensional accuracy of the pad, and achieve the effects of easy realization, high processing efficiency and simple process flow.
- Summary
- Abstract
- Description
- Claims
- Application Information
AI Technical Summary
Problems solved by technology
Method used
Image
Examples
specific Embodiment approach 1
[0023] Specific implementation mode one: combine Figure 1-Figure 3 Describe this embodiment, the described method for processing a bearing pad, the method is realized according to the following steps:
[0024] Step 1: Prepare the blank, the outer surface of the blank is a circular forging;
[0025] Step 2: Turning: turn the inner hole of the forging, and roughly machine the outer circle and end face of the forging;
[0026] Step 3: Pouring the bearing alloy at the inner hole of the forging;
[0027] Step 4: Semi-finishing machining: semi-finishing the inner hole, outer circle and end face, leaving a machining allowance on each side;
[0028] Step 5: Aging treatment: place the workpiece after semi-finishing in step 4 in an environment of 15-30 degrees Celsius for 72 hours;
[0029] Step 6: Finish turning the end face, semi-finishing the inner hole and outer circle: based on the inner hole, process the outer circle surface, leave milling allowance, and finish turning the end...
specific Embodiment approach 2
[0036] Specific implementation mode two: combination Figure 1-Figure 2 Describe this embodiment, a bearing pad processing method described in this embodiment, the inner hole of the forging is processed by semi-finishing in step 4, the radius of the inner hole is left with a machining allowance of 2 mm, and the radius of the outer circle is left with a machining allowance 1mm, each end face processing allowance is 0.5mm. Other compositions and connection methods are the same as those in Embodiment 1.
specific Embodiment approach 3
[0037] Specific implementation mode three: combination Figure 1-Figure 2 This embodiment is described, a bearing pad processing method described in this embodiment, in step 6, a machining allowance of 0.5 mm is left for the radius of the outer circle of the forging, and a machining allowance of 1.5 mm is left for the radius of the inner hole. Other compositions and connection methods are the same as those in Embodiment 1.
PUM
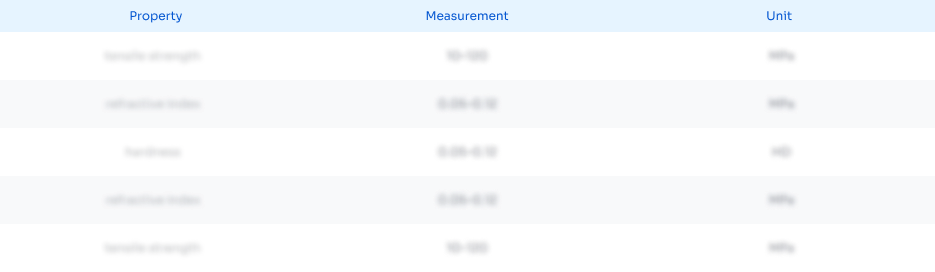
Abstract
Description
Claims
Application Information

- R&D
- Intellectual Property
- Life Sciences
- Materials
- Tech Scout
- Unparalleled Data Quality
- Higher Quality Content
- 60% Fewer Hallucinations
Browse by: Latest US Patents, China's latest patents, Technical Efficacy Thesaurus, Application Domain, Technology Topic, Popular Technical Reports.
© 2025 PatSnap. All rights reserved.Legal|Privacy policy|Modern Slavery Act Transparency Statement|Sitemap|About US| Contact US: help@patsnap.com