Scaling powder fluid pressure control device
A fluid pressure and control device technology, applied in the field of welding processing, can solve the problems of poor welding quality, poor welding, flux bubble interference, etc., and achieve the effects of improving the dissolution effect, simple structure and high stability
- Summary
- Abstract
- Description
- Claims
- Application Information
AI Technical Summary
Problems solved by technology
Method used
Image
Examples
Embodiment Construction
[0036] In order to make the object, technical solution and advantages of the present invention clearer, the present invention will be further described in detail below in combination with specific embodiments and with reference to the accompanying drawings. It should be noted that, in the case of no conflict, the embodiments of the present invention and the features in the embodiments can be combined with each other.
[0037] It is understood that these descriptions are exemplary only, and are not intended to limit the scope of the invention.
[0038] A flux fluid pressure control device provided by some embodiments of the present invention is described below with reference to the accompanying drawings.
[0039] combine Figure 1-7As shown, a flux fluid pressure control device provided by the present invention includes: a pressure stabilizing pump box 100, a defoaming valve group 200, and an active conveying assembly 300. A conveying cavity 101 is provided inside the stabiliz...
PUM
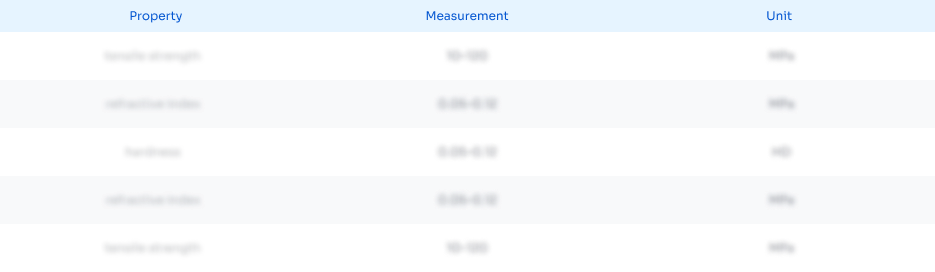
Abstract
Description
Claims
Application Information

- R&D
- Intellectual Property
- Life Sciences
- Materials
- Tech Scout
- Unparalleled Data Quality
- Higher Quality Content
- 60% Fewer Hallucinations
Browse by: Latest US Patents, China's latest patents, Technical Efficacy Thesaurus, Application Domain, Technology Topic, Popular Technical Reports.
© 2025 PatSnap. All rights reserved.Legal|Privacy policy|Modern Slavery Act Transparency Statement|Sitemap|About US| Contact US: help@patsnap.com