Device and method for preparing fine-particle-size powder high-temperature alloy hot isostatic pressing part
A technology of isostatic pressing and high temperature alloy, applied in the field of static pressing parts, can solve the problems of insufficient recrystallization driving force, lower yield, insufficient deformation, etc., to solve the problem of original particle boundary, reduce powder surface segregation, Guaranteed uniform distribution
- Summary
- Abstract
- Description
- Claims
- Application Information
AI Technical Summary
Problems solved by technology
Method used
Image
Examples
Embodiment 1
[0053] This embodiment provides a method of applying the above-mentioned device to prepare a hot isostatic pressed product of a fine-grained powder superalloy, which specifically includes the following steps:
[0054] Step 1: Prepare superalloy powder with fine particle size by gas atomization method or plasma rotating electrode method;
[0055] Step 2: Use the powder loading tank 1 to put the fine-grained superalloy powder into the bag 7 through the powder lower pipe 2. When the powder is loaded into the bag 7, the vacuum degree in the device body 3 is less than 0.01Pa, and the heat preservation of the bag 7 The temperature is 500°C, the powder feeding rate is 20kg / h, and the vibration frequency is 30Hz;
[0056] Step 3: After the powder is full, turn off the vacuum pump group 5 and fill in CO gas until the pressure in the device body 3 is 0.02 MPa, heat the jacket 7 to 600°C, and keep it warm for 3 hours; wherein, the purity of the CO gas is greater than or equal to 99.999%;...
Embodiment 2
[0060] This embodiment provides a method of applying the above-mentioned device to prepare a hot isostatic pressed product of a fine-grained powder superalloy, which specifically includes the following steps:
[0061] Step 1: Prepare superalloy powder with fine particle size by gas atomization method or plasma rotating electrode method;
[0062] Step 2: Use the powder loading tank 1 to put the fine-grained superalloy powder into the bag 7 through the powder lower pipe 2. When the powder is loaded into the bag 7, the vacuum degree in the device body 3 is less than 0.01Pa, and the heat preservation of the bag 7 The temperature is 550°C, the powder feed rate is 25kg / h, and the vibration frequency is 40Hz;
[0063] Step 3: After the powder is full, turn off the vacuum pump group 5 and fill in CO gas until the pressure in the device body 3 is 0.025 MPa, heat the envelope 7 to 700°C, and keep it warm for 2.5 hours; the purity of CO gas is greater than or equal to 99.999% ;
[0064...
Embodiment 3
[0067] This embodiment provides a method of applying the above-mentioned device to prepare a hot isostatic pressed product of a fine-grained powder superalloy, which specifically includes the following steps:
[0068] Step 1: Prepare superalloy powder with fine particle size by gas atomization method or plasma rotating electrode method;
[0069] Step 2: Use the powder loading tank 1 to put the fine-grained superalloy powder into the sheath through the powder lowering pipe 2. When the powder is loaded into the sheath 7, the vacuum degree in the device body 3 is less than 0.01Pa, and the heat preservation temperature of the sheath 7 The temperature is 600℃, the feeding rate is 30kg / h, and the vibration frequency is 50Hz;
[0070] Step 3: After the powder is full, turn off the vacuum pump group 5 and fill in CO gas until the pressure in the device body 3 is 0.03 MPa, heat the envelope 7 to 900°C, and keep it warm for 2 hours; wherein, the purity of the CO gas is greater than or e...
PUM
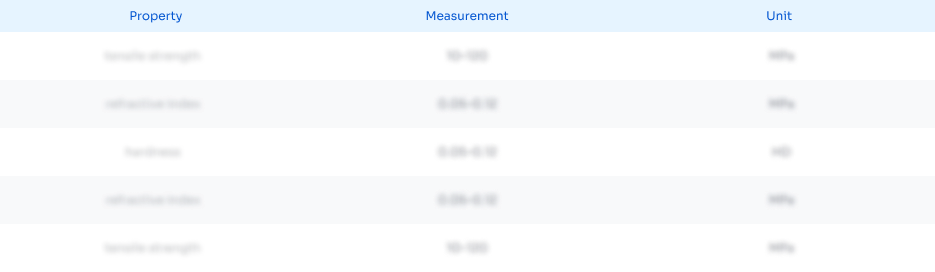
Abstract
Description
Claims
Application Information

- Generate Ideas
- Intellectual Property
- Life Sciences
- Materials
- Tech Scout
- Unparalleled Data Quality
- Higher Quality Content
- 60% Fewer Hallucinations
Browse by: Latest US Patents, China's latest patents, Technical Efficacy Thesaurus, Application Domain, Technology Topic, Popular Technical Reports.
© 2025 PatSnap. All rights reserved.Legal|Privacy policy|Modern Slavery Act Transparency Statement|Sitemap|About US| Contact US: help@patsnap.com