Lithium ion battery composite binder and preparation method and application thereof
A lithium-ion battery and binder technology, applied in battery electrodes, circuits, electrical components, etc., can solve the problems of increased internal resistance of batteries, reduced service life of lithium batteries, and reduced mobility of molecular segments, and reduced vitrification. temperature, enhancing surface force, avoiding the effect of conductive agent agglomeration
- Summary
- Abstract
- Description
- Claims
- Application Information
AI Technical Summary
Problems solved by technology
Method used
Image
Examples
Embodiment 1
[0038] The lithium-ion battery composite binder provided in this embodiment includes binder component A and binder component B, and binder component A is composed of sodium alginate (SA), polyvinyl alcohol (PVA) and polyvinyl alcohol (PVA) Acrylic acid (PAA) is prepared by compounding with carbon nanotube aqueous dispersion liquid after cross-linking reaction; B component of binder is PVA modified rubber emulsion.
[0039] The mass ratio of binder component A to binder component B is 2:1.
[0040] The preparation method of the lithium-ion battery composite binder of the present embodiment comprises the following steps:
[0041]S1. Put 1 part of sodium alginate, 30 parts of acrylic acid and 99 parts of deionized water into a beaker, and stir evenly; after the addition, let the solution stand at -10°C for 12 hours; vacuum degassing to obtain a mixed solution.
[0042] S2. Put 1.3 parts of polyvinyl alcohol and 38 parts of deionized water into a beaker, and stir at 90° C. for 2 ...
Embodiment 2
[0047] The difference between Example 2 and Example 1 is that the mass ratio of the binder component A to the binder component B is 5:1.
[0048] The preparation method of the lithium-ion battery composite binder of the present embodiment comprises the following steps:
[0049] S1. Put 1 part of sodium alginate, 35 parts of acrylic acid and 99 parts of deionized water into a beaker, and stir evenly; after the addition, let the solution stand at -12°C for 12 hours; vacuum defoaming to obtain a mixed solution.
[0050] S2. Put 1.7 parts of polyvinyl alcohol and 50 parts of deionized water into a beaker, and stir at 90° C. for 2 hours to obtain a polyvinyl alcohol solution.
[0051] S3. Mix the solutions of steps S1 and S2 evenly, then add 0.5 parts of ammonium persulfate and 0.5 parts of N,N-methylenebisacrylamide, and react at 80° C. for 4 hours to obtain a SA / PVA / PAA solution.
[0052] S4. Add 375 parts of the carbon nanotube aqueous dispersion to the SA / PVA / PAA solution in s...
Embodiment 3
[0055] The difference between Example 3 and Example 1 is that the mass ratio of the binder component A to the binder component B is 10:1.
[0056] The preparation method of the lithium-ion battery composite binder of the present embodiment comprises the following steps:
[0057] S1. Put 5 parts of sodium alginate, 35 parts of acrylic acid and 99 parts of deionized water into a beaker, and stir evenly; after the addition, let the solution stand at -12°C for 16 hours; vacuum defoaming to obtain a mixed solution.
[0058] S2. Put 2 parts of polyvinyl alcohol and 58 parts of deionized water into a beaker, and stir at 90° C. for 2 hours to obtain a polyvinyl alcohol solution.
[0059] S3. Mix the solutions of steps S1 and S2 evenly, then add 1 part of ammonium persulfate and 1 part of N,N-methylenebisacrylamide, and react at 80° C. for 2 hours to obtain a SA / PVA / PAA solution.
[0060] S4. Add 201 parts of the carbon nanotube aqueous dispersion to the SA / PVA / PAA solution in step S3...
PUM
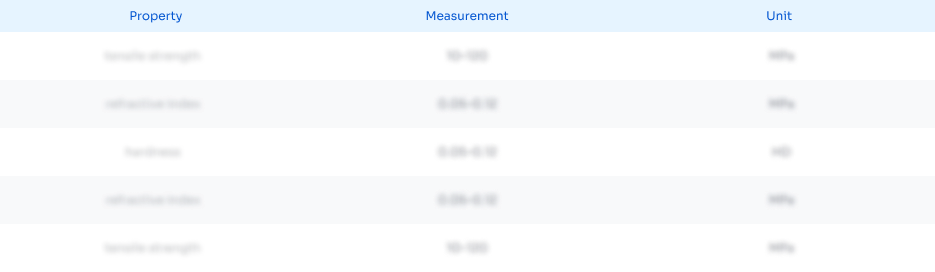
Abstract
Description
Claims
Application Information

- R&D Engineer
- R&D Manager
- IP Professional
- Industry Leading Data Capabilities
- Powerful AI technology
- Patent DNA Extraction
Browse by: Latest US Patents, China's latest patents, Technical Efficacy Thesaurus, Application Domain, Technology Topic, Popular Technical Reports.
© 2024 PatSnap. All rights reserved.Legal|Privacy policy|Modern Slavery Act Transparency Statement|Sitemap|About US| Contact US: help@patsnap.com