X-ray flaw detection intelligent detection method
A technology of intelligent detection and radiographic flaw detection, applied in measurement devices, material analysis using radiation, material analysis using wave/particle radiation, etc. The effect of improving labor productivity, reducing defect missed detection rate, and reducing workload
- Summary
- Abstract
- Description
- Claims
- Application Information
AI Technical Summary
Problems solved by technology
Method used
Image
Examples
Embodiment Construction
[0067] According to an embodiment of the present invention, an intelligent detection method for X-ray flaw detection is provided.
[0068] Now in conjunction with accompanying drawing and specific embodiment the present invention is further described, as Figure 1-Figure 2 As shown, according to the X-ray flaw detection intelligent detection method of the embodiment of the present invention, the method includes the following steps:
[0069] S1, using X-ray detection equipment to carry out real-time dynamic detection of steel pipes;
[0070] S2. The computer receives the dynamic image in real time, and sets the window level and window width of the dynamic image;
[0071] Wherein, the method for setting the window level and window width of the dynamic image includes one-key automatic adjustment, mouse movement modification and manual value modification.
[0072] The one-key automatic adjustment setting the window level and window width of the dynamic image includes the followi...
PUM
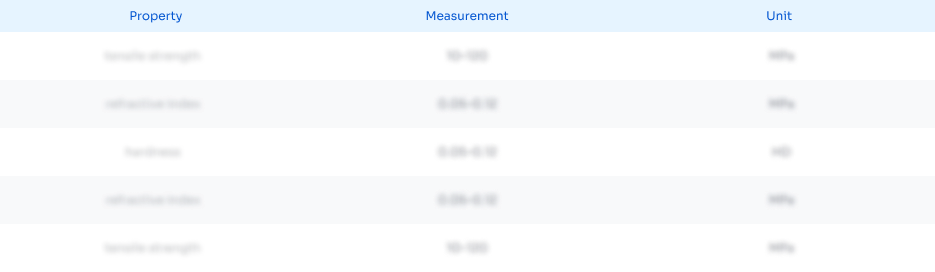
Abstract
Description
Claims
Application Information

- R&D
- Intellectual Property
- Life Sciences
- Materials
- Tech Scout
- Unparalleled Data Quality
- Higher Quality Content
- 60% Fewer Hallucinations
Browse by: Latest US Patents, China's latest patents, Technical Efficacy Thesaurus, Application Domain, Technology Topic, Popular Technical Reports.
© 2025 PatSnap. All rights reserved.Legal|Privacy policy|Modern Slavery Act Transparency Statement|Sitemap|About US| Contact US: help@patsnap.com