Ultrasonic co-frequency observation device and method for directly displaying second modal waves
A technology of observation device and detection device, which is applied in the direction of measuring device, machine/structural component testing, aircraft component testing, etc., and can solve the problems of high price, limited spatial resolution, inability to realize direct measurement and display of the second modal wave, etc. , to achieve the effect of simple installation
- Summary
- Abstract
- Description
- Claims
- Application Information
AI Technical Summary
Problems solved by technology
Method used
Image
Examples
Embodiment Construction
[0023] The following will clearly and completely describe the technical solutions in the embodiments of the present invention with reference to the accompanying drawings in the embodiments of the present invention. Obviously, the described embodiments are only some, not all, embodiments of the present invention. Based on the embodiments of the present invention, all other embodiments obtained by persons of ordinary skill in the art without making creative efforts belong to the protection scope of the present invention.
[0024] The invention discloses an ultrasonic co-frequency observation device for direct display of the second mode, which is mainly aimed at the observation of the second mode wave in the hypersonic boundary layer, adopts an ultrasonic co-frequency LED light source, and uses a signal generator to control the LED The frequency of the light source makes it differ from the frequency of the second modal wave by a few hertz, and the spatial distribution of the secon...
PUM
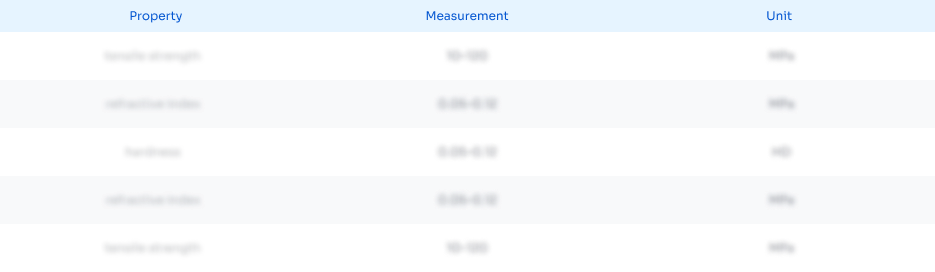
Abstract
Description
Claims
Application Information

- Generate Ideas
- Intellectual Property
- Life Sciences
- Materials
- Tech Scout
- Unparalleled Data Quality
- Higher Quality Content
- 60% Fewer Hallucinations
Browse by: Latest US Patents, China's latest patents, Technical Efficacy Thesaurus, Application Domain, Technology Topic, Popular Technical Reports.
© 2025 PatSnap. All rights reserved.Legal|Privacy policy|Modern Slavery Act Transparency Statement|Sitemap|About US| Contact US: help@patsnap.com