A kind of inner cavity web processing method
A processing method and web technology, applied in the field of aerospace metal cutting, can solve the problems of cumbersome processing process and poor processing accuracy, achieve the effect of no manual intervention, improve processing efficiency and processing accuracy, and meet processing requirements
- Summary
- Abstract
- Description
- Claims
- Application Information
AI Technical Summary
Problems solved by technology
Method used
Image
Examples
Embodiment 1
[0038] see Figure 1-Figure 2 , a method for processing an inner cavity web, comprising the steps of:
[0039] a. Position and clamp the part 1 to be processed through the process boss 2;
[0040] b. Find the processing coordinate system 3 of the part 1 to be processed;
[0041] c. Rough machining the front side 6 of the inner cavity web and the reverse side 7 of the inner cavity web of the part 1 to be processed, leaving a part of the margin as the remaining material area of the inner cavity web;
[0042] d. Finishing the reverse side 7 of the inner cavity web of the part 1 to be processed to the preset size;
[0043] e. After processing the reverse side 7 of the inner cavity web of the part 1 to be processed to the preset size, then process the front side 4 of the inner cavity web verification area and the reverse side 5 of the inner cavity web verification area;
[0044] f. Call the probe on the machine tool to measure the actual thickness of the front side 4 of the in...
Embodiment 2
[0048] see Figure 1-Figure 2 , a method for processing an inner cavity web, comprising the steps of:
[0049] a. Position and clamp the part 1 to be processed through the process boss 2;
[0050] b. Find the processing coordinate system 3 of the part 1 to be processed;
[0051] c. Rough machining the front side 6 of the inner cavity web and the reverse side 7 of the inner cavity web of the part 1 to be processed, leaving a part of the margin as the remaining material area of the inner cavity web;
[0052] d. Finishing the reverse side 7 of the inner cavity web of the part 1 to be processed to the preset size;
[0053] e. After processing the reverse side 7 of the inner cavity web of the part 1 to be processed to the preset size, then process the front side 4 of the inner cavity web verification area and the reverse side 5 of the inner cavity web verification area;
[0054] f. Call the probe on the machine tool to measure the actual thickness of the front side 4 of the in...
Embodiment 3
[0058] see Figure 1-Figure 2 , a method for processing an inner cavity web, comprising the steps of:
[0059] a. Position and clamp the part 1 to be processed through the process boss 2;
[0060] b. Find the processing coordinate system 3 of the part 1 to be processed;
[0061] c. Rough machining the front side 6 of the inner cavity web and the reverse side 7 of the inner cavity web of the part 1 to be processed, leaving a part of the margin as the remaining material area of the inner cavity web;
[0062] d. Finishing the reverse side 7 of the inner cavity web of the part 1 to be processed to the preset size;
[0063] e. After processing the reverse side 7 of the inner cavity web of the part 1 to be processed to the preset size, then process the front side 4 of the inner cavity web verification area and the reverse side 5 of the inner cavity web verification area;
[0064] f. Call the probe on the machine tool to measure the actual thickness of the front side 4 of the in...
PUM
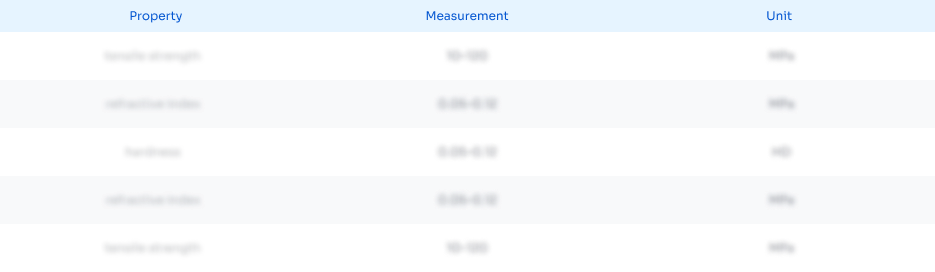
Abstract
Description
Claims
Application Information

- Generate Ideas
- Intellectual Property
- Life Sciences
- Materials
- Tech Scout
- Unparalleled Data Quality
- Higher Quality Content
- 60% Fewer Hallucinations
Browse by: Latest US Patents, China's latest patents, Technical Efficacy Thesaurus, Application Domain, Technology Topic, Popular Technical Reports.
© 2025 PatSnap. All rights reserved.Legal|Privacy policy|Modern Slavery Act Transparency Statement|Sitemap|About US| Contact US: help@patsnap.com