Rotary detachable steel frame and laminated slab connecting structure
A technology for connecting structures and laminated boards, which is applied to floors, building components, building structures, etc., can solve the problems of increased construction measures cost, low construction efficiency, inconvenient disassembly and reuse of temporary supports, etc. Easy to install, suitable for widespread promotion and application
- Summary
- Abstract
- Description
- Claims
- Application Information
AI Technical Summary
Problems solved by technology
Method used
Image
Examples
Embodiment 1
[0064] Such as Figure 1~4 as well as Figure 37 The connection structure between the rotating detachable steel frame and the laminated slab shown includes a prefabricated bottom slab 2, a cast-in-place concrete layer 1 poured on the prefabricated bottom slab 2, and a number of square steel pipes 3 detachably fixed on the prefabricated bottom slab 2 for support. ; The square steel pipes 3 are longitudinally arranged along the prefabricated floor 2 and arranged side by side. A square hole 31 is provided on the side of the square steel pipe 3 away from the prefabricated bottom plate 2, a steel pipe hole 33 is provided on the square steel pipe 3 on the side opposite to the square hole 31, and a bottom plate hole through which both sides are connected is provided on the prefabricated bottom plate 2 corresponding to the steel pipe hole 33. 21; the steel pipe hole 33 and the corresponding bottom plate hole 21 are installed with a large Π-shaped embedded part 4, a T-shaped connector...
Embodiment 2
[0069] Such as Figure 13 , 16 The structural schematic diagram of the embedded part shown in ~ 18, the difference between the second embodiment and the first embodiment is that the embedded part 4 includes a cylindrical embedded part body 45, a round body integrally formed and installed on the top of the embedded part body 45 Shaped bottom plate 41 and 8 steel bars 47 that are evenly welded in the middle part of the embedded part cylinder body 45 . The design of the steel bar 47 enhances the connection stability between the embedded part 4 and the prefabricated bottom plate 2 , and facilitates the bonding of the prefabricated bottom plate 2 and the embedded part 4 .
Embodiment 3
[0071] Such as Figure 19-20 , 23-24 and 26-27 show the structural schematic diagrams of the embedded parts. The difference between the third embodiment and the first embodiment is that the embedded part 4 includes a cylindrical embedded part body 45, which is set on the embedded part body. The hoisting hole 46 at the top of 45 and the annular plate 43 integrally formed on the middle part of the pre-embedded body 45 . Eight fan-shaped locking teeth I 44 are uniformly formed on the inner wall of the embedded part cylinder body 45, and the central angle of the locking teeth I 44 is 22.5°. Eight through-holes 42 are evenly opened on the annular plate 43. When the prefabricated bottom plate 2 is prefabricated, part of the slurry flows through the through-holes 42, which facilitates the bonding of the prefabricated bottom plate 2 and the embedded parts 4, and improves the installation stability of the embedded parts 4. . At the same time, the design of the annular plate 43 also e...
PUM
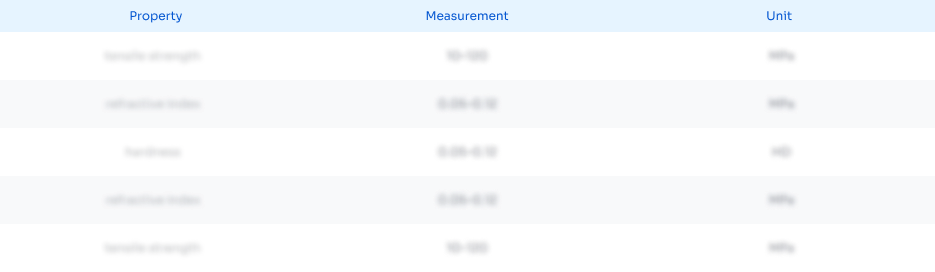
Abstract
Description
Claims
Application Information

- R&D
- Intellectual Property
- Life Sciences
- Materials
- Tech Scout
- Unparalleled Data Quality
- Higher Quality Content
- 60% Fewer Hallucinations
Browse by: Latest US Patents, China's latest patents, Technical Efficacy Thesaurus, Application Domain, Technology Topic, Popular Technical Reports.
© 2025 PatSnap. All rights reserved.Legal|Privacy policy|Modern Slavery Act Transparency Statement|Sitemap|About US| Contact US: help@patsnap.com