Automatic alignment method and device using optical alignment
An automatic alignment and optical technology, applied in the field of manufacturing and processing, can solve the problems of automatic operation interruption, affecting equipment operation, reducing production output, etc., to achieve the effect of high alignment success rate, saving time and ensuring stability.
- Summary
- Abstract
- Description
- Claims
- Application Information
AI Technical Summary
Problems solved by technology
Method used
Image
Examples
Embodiment Construction
[0034] Such as Figure 1-Figure 2 Shown: an automatic alignment method using optical alignment, including a grooved workpiece 1 to be aligned and an optical transceiver module, the optical transceiver module includes a first transmitting end, a second transmitting end, a first receiving end and a second The receiving end, the first transmitting end, the second transmitting end, the third transmitting end, and the fourth transmitting end are all arranged on the same horizontal plane, and the first transmitting end and the second receiving end are arranged on one side of the workpiece, and the first receiving end and the second emitting end are respectively located on the other side of the workpiece,
[0035] Mark the first reference point, the second reference point, the third reference point, and the fourth reference point on the workpiece, and the first reference point, the second reference point, the third reference point, and the fourth reference point are all located on th...
PUM
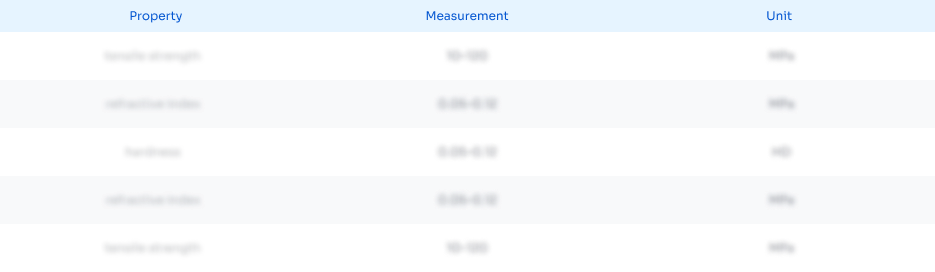
Abstract
Description
Claims
Application Information

- Generate Ideas
- Intellectual Property
- Life Sciences
- Materials
- Tech Scout
- Unparalleled Data Quality
- Higher Quality Content
- 60% Fewer Hallucinations
Browse by: Latest US Patents, China's latest patents, Technical Efficacy Thesaurus, Application Domain, Technology Topic, Popular Technical Reports.
© 2025 PatSnap. All rights reserved.Legal|Privacy policy|Modern Slavery Act Transparency Statement|Sitemap|About US| Contact US: help@patsnap.com