Carbon fiber cold and hot wire joint of hinging process and hinging forming process of carbon fiber cold and hot wire joint
A molding process, cold and hot wire technology, applied in hot-dip plating process, metal material coating process, connection, etc., can solve the problems of poor electrical conductivity, increase the current conduction area of carbon fiber filaments, reduce contact resistance, etc., and achieve low cost, High reliability and the effect of reducing contact resistance
- Summary
- Abstract
- Description
- Claims
- Application Information
AI Technical Summary
Problems solved by technology
Method used
Examples
Embodiment 1
[0028] The pretreatment is mainly to obtain carbon fiber wires and metal wires. Generally, carbon fiber heating wires and metal wires have a multi-layer structure. In this embodiment, the structure of carbon fiber heating wires is PVC anti-corrosion layer, poly Vinyl insulation, silicone insulation and carbon fiber filaments. The structure of the metal wire is a pvc anti-corrosion layer, a polyethylene insulation layer and a tinned copper wire from the outside to the inside.
[0029] In this embodiment, the pretreatment is mainly to peel off the outer multilayer structure of the carbon fiber heating wire and the metal wire, that is, to peel off the pvc anticorrosion layer, polyethylene insulation layer and silica gel insulation layer of the carbon fiber heating wire and metal wire , peel off the multi-layer structure of the outer layer of carbon fiber filaments, and do pretreatment for subsequent connection realization.
[0030] Specifically: Use peeling equipment to peel off...
Embodiment 2
[0055] The difference from embodiment 1 is that embodiment 2 provides a carbon fiber cold and hot wire joint forming process without the need to attach flux. That is to say, the method provided in this embodiment is different from that in Embodiment 1 in obtaining the tinned copper wire.
[0056] The processing technology of the tinned copper wire provided by the present embodiment comprises the following specific steps:
[0057] (1) Carry out cathodic protection to the copper wire after the pickling treatment and lead it into the tin pool, after fully immersing, make the copper wire pass through the tinned eye mold, and lead out the tinned copper wire vertically upward;
[0058] (2) The lead-out tinned copper wires were sequentially cooled by about 15°C at a cooling rate of 7°C / min, and then further cooled and pulled at a cooling rate of 15°C / min to obtain finished tinned copper wires.
[0059] In this embodiment, the first composite yarn is obtained by inserting, dividing a...
Embodiment 3
[0065] (1) Carry out cathodic protection to the copper wire after the pickling treatment and lead it into the tin pool, after fully immersing, make the copper wire pass through the tinned eye mold, and lead out the tinned copper wire vertically upward;
[0066] (2) Cool the exported tinned copper wire by about 15°C at a cooling rate of 10°C / min, and then further cool and pull it at a cooling rate of 30°C / min, add guide shaft oil and take up the wire to obtain the finished tinned copper wire copper wire.
PUM
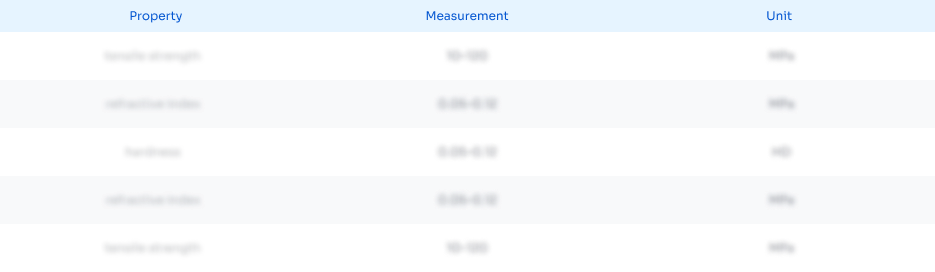
Abstract
Description
Claims
Application Information

- R&D Engineer
- R&D Manager
- IP Professional
- Industry Leading Data Capabilities
- Powerful AI technology
- Patent DNA Extraction
Browse by: Latest US Patents, China's latest patents, Technical Efficacy Thesaurus, Application Domain, Technology Topic, Popular Technical Reports.
© 2024 PatSnap. All rights reserved.Legal|Privacy policy|Modern Slavery Act Transparency Statement|Sitemap|About US| Contact US: help@patsnap.com