Brightener for PSA electrotinning insoluble anode system and application
A soluble anode and electro-tin plating technology, which is applied in the field of brighteners, can solve problems such as turbidity of the plating solution, tin mud, stains on the surface of the tin plate, etc., and achieve uniform and refined coating grains, excellent corrosion resistance, and not easy to be oxidized Effect
- Summary
- Abstract
- Description
- Claims
- Application Information
AI Technical Summary
Problems solved by technology
Method used
Examples
Embodiment 1
[0029] The brightener used for PSA electroplating tin insoluble anode system in the present embodiment comprises the following components by weight percentage: imidazoline 10%, 3-alkyl-4-amino-5-mercapto-1,2,4 - 20% of s-triazole, 25% of polyethylene glycol, 35% of alkamide polyoxyethylene ether, 2% of p-di-tert-butylpyrocatechol, 8% of triethylenetetraminehexaacetic acid, the above raw materials are weighed in proportion Take it out and mix it evenly to get the brightener for PSA electroplating tin insoluble anode system.
[0030] In the electroplating solution of the PSA electroplating tin insoluble anode system at a temperature of 30°C, add 3% of the brightener for the PSA electroplating tin insoluble anode system, and the current density is 3mA / cm 2 Electroplating is carried out under certain conditions to obtain a bright coating with uniform and refined grains.
[0031]For the coating obtained in the above electroplating process and the electroplating solution after elec...
Embodiment 2
[0033] The brightener used for PSA electroplating tin insoluble anode system in the present embodiment comprises the following components by weight percentage: imidazoline 20%, 3-alkyl-4-amino-5-mercapto-1,2,4 - 20% of s-triazole, 10% of polyethylene glycol, 20% of alkamide polyoxyethylene ether, 5% of p-di-tert-butylpyrocatechol, 5% of triethylenetetraminehexaacetic acid, the above raw materials are weighed in proportion Take it out and mix it evenly to get the brightener for PSA electroplating tin insoluble anode system.
[0034] In the electroplating solution of the PSA electroplating tin insoluble anode system at a temperature of 30°C, add 4% of the brightener for the PSA electroplating tin insoluble anode system, and the current density is 3mA / cm 2 Electroplating is carried out under certain conditions to obtain a bright coating with uniform and refined grains.
[0035] For the coating obtained in the above electroplating process and the electroplating solution after ele...
Embodiment 3
[0037] The brightener that is used for PSA electroplating tin insoluble anode system in the present embodiment comprises the following components by weight percentage: imidazoline 15%, 3-alkyl-4-amino-5-mercapto-1,2,4 - 15% of s-triazole, 30% of polyethylene glycol, 30% of alkamide polyoxyethylene ether, 3% of p-di-tert-butylpyrocatechol, 7% of triethylenetetraminehexaacetic acid, the above raw materials are weighed in proportion Take it out and mix it evenly to get the brightener for PSA electroplating tin insoluble anode system.
[0038] In the PSA electroplating tin insoluble anode system electroplating solution at a temperature of 30°C, add 5% of the brightener for the PSA electroplating tin insoluble anode system, and the current density is 3mA / cm 2 Electroplating is carried out under certain conditions to obtain a bright coating with uniform and refined grains.
[0039] For the coating obtained in the above electroplating process and the electroplating solution after el...
PUM
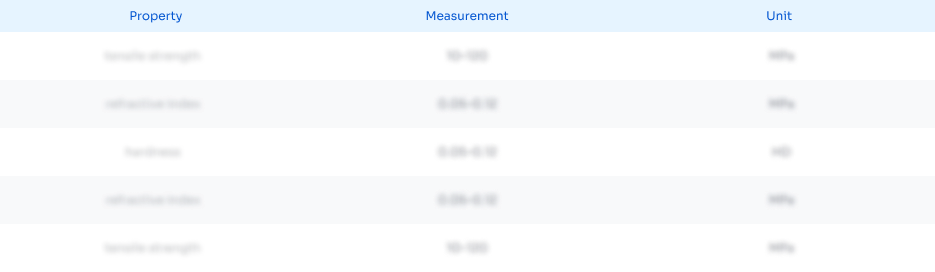
Abstract
Description
Claims
Application Information

- R&D Engineer
- R&D Manager
- IP Professional
- Industry Leading Data Capabilities
- Powerful AI technology
- Patent DNA Extraction
Browse by: Latest US Patents, China's latest patents, Technical Efficacy Thesaurus, Application Domain, Technology Topic, Popular Technical Reports.
© 2024 PatSnap. All rights reserved.Legal|Privacy policy|Modern Slavery Act Transparency Statement|Sitemap|About US| Contact US: help@patsnap.com