Solar backboard protective film and preparation process thereof
The invention relates to a technology for a solar back sheet and a preparation process, which is applied in the field of a solar back sheet protective film and its preparation technology, and can solve the problems of high price of imported transparent fluorine film, low light transmittance of the transparent fluorine film, insufficient weather resistance and the like, and achieve good hardness. , reduce energy consumption and cost, increase the effect of output
- Summary
- Abstract
- Description
- Claims
- Application Information
AI Technical Summary
Problems solved by technology
Method used
Image
Examples
Embodiment 1
[0053]Step S1: first put 10g GU6300N, 10g GU1700P, 50g GU9315Z, 20g GU2500K into the stirring tank, stir evenly and heat;
[0054] Step S2: Then add 0.2g Irganox1010, 0.5g Tinuvin326 and 0.5g Tinuvin292 into the stirred tank, and keep stirring at constant temperature;
[0055] Step S3: Then add 0.1g Efka 2020 and 0.1g Efka 3600 into the stirred tank, and stir evenly to obtain the protective layer composition;
[0056] Step S4: Coating the protective layer composition on the base layer 1, forming a wet film of the composition protective layer 2 with a thickness of 10 microns on the surface of the base layer 1, using a voltage of 150kv, a dose of 30KGy, and controlling the oxygen content at 200PPm. Beam radiation curing film.
Embodiment 2
[0058] Step S1: First put 20g GU6300N, 10g GU1700P, 50g GU9315Z, 10g GU2500K into the stirring tank, stir evenly and heat;
[0059] Step S2: Then add 0.2g Irganox1010, 0.5g Tinuvin326 and 0.5g Tinuvin292 into the stirred tank, and keep stirring at constant temperature;
[0060] Step S3: Then add 0.1g Efka 2020 and 0.1g Efka 3600 into the stirred tank, and stir evenly to obtain the protective layer composition;
[0061] Step S4: Coating the protective layer composition on the base layer 1, forming a wet film of the composition protective layer 2 with a thickness of 10 microns on the surface of the base layer 1, using a voltage of 150kv, a dose of 30KGy, and controlling the oxygen content at 200PPm. Beam radiation curing film.
Embodiment 3
[0063] Step S1: first put 30g GU6300N, 60g GU9315Z, 10g GU2500K into the stirring tank, stir evenly and heat;
[0064] Step S2: Then add 0.2g Irganox1010, 0.5g Tinuvin326 and 0.5g Tinuvin292 into the stirred tank, and keep stirring at constant temperature;
[0065] Step S3: Then add 0.1g Efka 2020 and 0.1g Efka 3600 into the stirred tank, and stir evenly to obtain the protective layer composition;
[0066] Step S4: Coating the protective layer composition on the base layer 1, forming a wet film of the composition protective layer 2 with a thickness of 10 microns on the surface of the base layer 1, using a voltage of 150kv, a dose of 30KGy, and controlling the oxygen content at 200PPm. Beam radiation curing film.
PUM
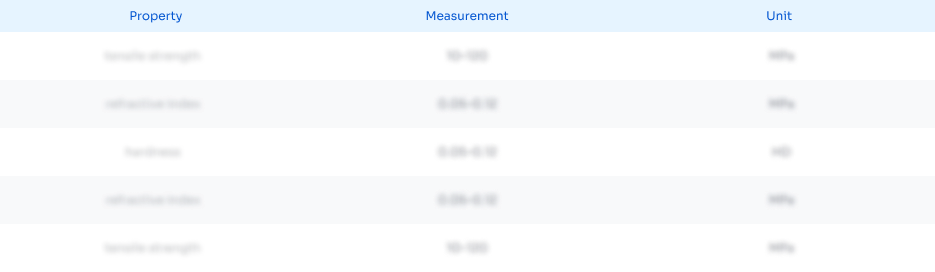
Abstract
Description
Claims
Application Information

- R&D
- Intellectual Property
- Life Sciences
- Materials
- Tech Scout
- Unparalleled Data Quality
- Higher Quality Content
- 60% Fewer Hallucinations
Browse by: Latest US Patents, China's latest patents, Technical Efficacy Thesaurus, Application Domain, Technology Topic, Popular Technical Reports.
© 2025 PatSnap. All rights reserved.Legal|Privacy policy|Modern Slavery Act Transparency Statement|Sitemap|About US| Contact US: help@patsnap.com