Preparation method of long-carbon-chain nylon and obtained nylon
A long carbon chain, nylon technology, applied in the field of polymer materials, can solve the problems of long carbon chain nylon with less polymer filler, unstable polymerization, easy to be oxidized, etc. long time effect
- Summary
- Abstract
- Description
- Claims
- Application Information
AI Technical Summary
Problems solved by technology
Method used
Image
Examples
Embodiment 1
[0073] Nylon salt formation: (1) Add 900.5g of dodecanedibasic acid and 4500g of ethanol into the neutralization kettle, heat to 75°C to dissolve, and keep for 30 minutes; (2) Add 783.5g of dodecanediamine Add 1000% ethanol into the dissolution tank, heat to 60°C to dissolve, and keep for 30 minutes; (3) Put all the dodecyl diamine ethanol solution into the neutralization tank through the pump, react while stirring, and control the reaction temperature At 78°C, continue to react for 1.0 hour after adding the materials, cool the neutralization tank to lower the temperature below 30°C, filter the neutralization solution through a filter, and dry in a drying oven to obtain nylon 1212 salt;
[0074] Polymerization of Nylon 1212: (1) Mix 600g of nylon 1212 salt with 600g of water, catalyst, molecular weight regulator, antioxidant, etc., and then add it to a 2.0L high-temperature and high-pressure polymerization kettle. The catalyst is sodium hypophosphite, and the molecular weight r...
Embodiment 2
[0076] Nylon salt-forming steps are the same as in Example 1.
[0077] Polymerization of Nylon 1212: (1) Mix 600g of Nylon 1212 salt with 900g of water, catalyst, molecular weight regulator, antioxidant, etc., and then add it to a 2.0L high-temperature and high-pressure polymerization kettle. Among them, sodium hypophosphite is selected as the catalyst, and laurel is selected as the molecular weight regulator. Acid and antioxidant select antioxidant 1098, the addition amount is 0.1wt%; (2) heat up to 210°C for 1.0h, and the pressure in the kettle rises to 1.8MPa, keep this temperature and pressure reaction for 2.0 hours; (3) Slowly deflate, make the pressure in the kettle maintain 1.8MPa in the first 1.0 hour, and then drop the pressure in the kettle to normal pressure in the next 1.0 hour; (4) keep the reaction temperature at 240° C. for 2.0 hours under normal pressure, stop stirring, Open the discharge valve, fill with nitrogen, the material flows out through the injection h...
Embodiment 3
[0079] Nylon salt-forming steps are the same as in Example 1.
[0080] Polymerization of Nylon 1212: (1) Mix 600g of nylon 1212 salt with 600g of water, catalyst, molecular weight regulator, antioxidant, etc., and then add it to a 2.0L high-temperature and high-pressure polymerization kettle. The catalyst is sodium hypophosphite, and the molecular weight regulator is lauryl. Acid and antioxidant select antioxidant 1098, and the addition amount is 0.1wt%; (2) heat up to 200°C for 1.0h, and the pressure in the kettle rises to 1.5MPa, and keep this temperature and pressure reaction for 2.0 hours; (3) Slowly deflate, make the pressure in the kettle maintain 1.5MPa in the first 1.0 hour, and then drop the pressure in the kettle to normal pressure in the next 1.0 hour; (4) keep the reaction temperature at 240° C. for 2.0 hours under normal pressure, stop stirring, Open the discharge valve, fill with nitrogen, the material flows out through the injection head, and after cooling, it i...
PUM
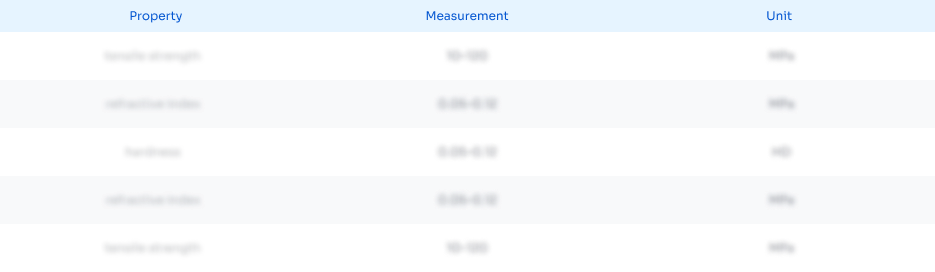
Abstract
Description
Claims
Application Information

- R&D Engineer
- R&D Manager
- IP Professional
- Industry Leading Data Capabilities
- Powerful AI technology
- Patent DNA Extraction
Browse by: Latest US Patents, China's latest patents, Technical Efficacy Thesaurus, Application Domain, Technology Topic, Popular Technical Reports.
© 2024 PatSnap. All rights reserved.Legal|Privacy policy|Modern Slavery Act Transparency Statement|Sitemap|About US| Contact US: help@patsnap.com