Nylon carbon fiber and preparation process thereof
A technology of nylon carbon fiber and preparation process, which is applied in the direction of fiber type, fiber treatment, fiber chemical characteristics, etc., can solve the problems that conductive fibers do not have anisotropy, it is difficult to achieve the effect of conductivity, and the plating layer is easy to be dissolved and removed. Achieve the effects of low density, easy packing, and enlarged micropore diameter
- Summary
- Abstract
- Description
- Claims
- Application Information
AI Technical Summary
Problems solved by technology
Method used
Image
Examples
preparation example Construction
[0041] The invention also discloses a preparation process of nylon carbon fiber, which includes the following steps: step S1, heating nylon material and carbon black material to form a melt, and transporting the two melts into the composite spinning assembly through their respective delivery pipelines , independently distributed and conveyed through the respective flow channels of the melt inside the composite spinning assembly, and finally extruded through the special-shaped hole at the exit of the composite spinning assembly, and entered into the cooling liquid for forming; S2 step, the formed nylon carbon fiber is passed through electromagnetic induction Heating by means of heating, so that the skin layer 2 in the nylon carbon fiber is heated to 20-50 ° C, and the heat source in the transition zone 3 is deposited, causing the surface of the core layer 1 to expand when heated, and the micropores on the surface are opened to form a sticky layer that is easy to adhere to the met...
Embodiment 2
[0047] There are multiple core layers 1, which are symmetrically distributed around the center of the skin layer 2. The core layer 1 is compounded with the skin layer 2 through a unique composite spinning assembly, so that the prepared preliminary nylon carbon fiber is evenly spaced and arranged with multiple pairs of transition regions 3, and can be processed on the nylon carbon fiber at the same time The multi-point coating improves the overall performance of nylon carbon fiber. While ensuring the weight of nylon carbon fiber itself, it can obtain more excellent ductility, conductivity, wear resistance and electromagnetic shielding ability.
[0048] Except for the above distinguishing features, other technical features refer to Embodiment 1 and will not be repeated here.
PUM
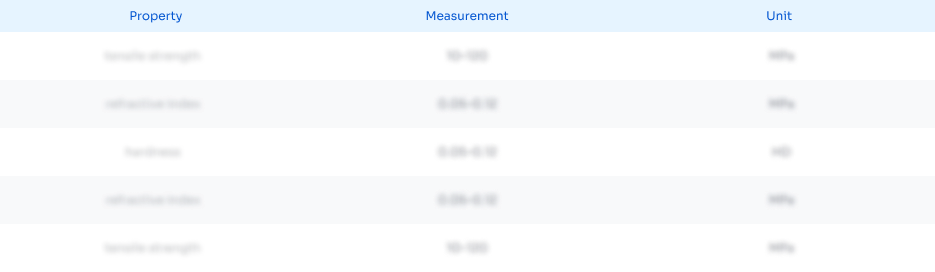
Abstract
Description
Claims
Application Information

- R&D Engineer
- R&D Manager
- IP Professional
- Industry Leading Data Capabilities
- Powerful AI technology
- Patent DNA Extraction
Browse by: Latest US Patents, China's latest patents, Technical Efficacy Thesaurus, Application Domain, Technology Topic, Popular Technical Reports.
© 2024 PatSnap. All rights reserved.Legal|Privacy policy|Modern Slavery Act Transparency Statement|Sitemap|About US| Contact US: help@patsnap.com