Preparation method of heat-preservation and heat-insulation cement
A technology of thermal insulation and production method, which is applied in the direction of filling slurry, etc., can solve the problems that cannot be solved at the same time, pollution, falling off, etc., and achieve the effect of increasing constructability, increasing weather resistance, and high tensile strength
- Summary
- Abstract
- Description
- Claims
- Application Information
AI Technical Summary
Problems solved by technology
Method used
Examples
Embodiment 1
[0020] A method for making heat-insulating active putty, comprising the following steps: weighing raw materials in corresponding parts by mass: 100 parts of 425# cement, 30 parts of 200-mesh active calcium powder, 20 parts of vegetable protein fiber with a fiber content of 95%, 30 parts of polystyrene particles with a diameter of 2, 10 parts of vitrified microbeads with a mesh number of 20, 3 parts of tackifier, 3 parts of HPMC, 5 parts of dispersible latex powder, and cement and active calcium powder of corresponding mass parts , natural mineral fiber, vegetable protein fiber, HPMC, dispersible latex powder are placed in the stirrer and fully mix 5min, obtain the first mixture, then add the vitrified microbead of corresponding mass fraction in the first mixture in the stirrer, again Start the mixer and stir and mix thoroughly for 5 minutes to obtain the second mixture. Put the second mixture into a packaging bag according to a certain weight, and add a corresponding mass of po...
Embodiment 2
[0023] A method for making heat-preserving and heat-insulating cement, comprising the following steps: weighing raw materials in corresponding parts by mass: 110 parts of 425# cement, 40 parts of 250-mesh active calcium powder, 25 parts of vegetable protein fibers with a fiber content of 96%, diameter 35 parts of polyphenylene particles of 2nm, 13 parts of vitrified microbeads of 40 meshes, 4 parts of tackifier, 4 parts of HPMC, 7 parts of dispersible latex powder, the corresponding mass parts of cement, active calcium powder, Natural mineral fiber, vegetable protein fiber, HPMC, latex powder are placed in the blender and fully mixed for 6min to obtain the first mixture, then add polyphenylene particles and vitrified microspheres of corresponding mass parts in the first mixture in the blender, and again Start the mixer and stir and mix thoroughly for 6 minutes to obtain the second mixture, put the second mixture into a packaging bag according to a certain weight, and add polyph...
Embodiment 3
[0026] A method for making heat-preserving and heat-insulating cement, comprising the following steps: weighing raw materials in corresponding parts by mass: 120 parts of 525# cement, 50 parts of active calcium powder above 300 mesh, and 30 parts of vegetable protein fiber with a fiber content of 98% , 40 parts of polystyrene particles with a diameter of 3nm, 15 parts of vitrified microbeads with a mesh number of 70, 5 parts of tackifier, 5 parts of HPMC, 10 parts of dispersible latex powder, cement and active calcium powder, natural mineral fiber, vegetable protein fiber, HPMC, and latex powder were placed in a blender and mixed thoroughly for 8 minutes to obtain the first mixture, and then polyphenylene particles and vitrified microspheres were added in corresponding parts by mass to the first mixture in the blender , and start the mixer again to fully stir and mix for 8 minutes to obtain the second mixture, put the second mixture into a packaging bag according to a certain w...
PUM
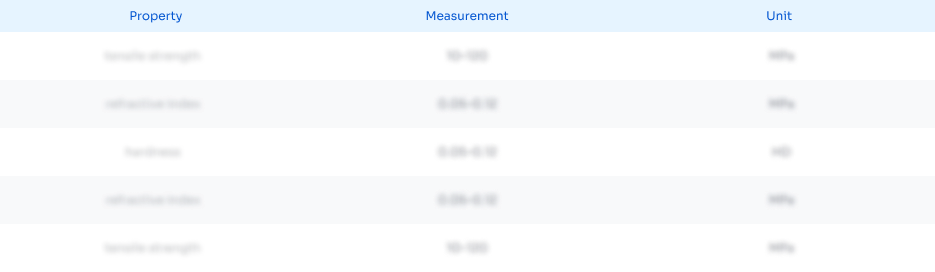
Abstract
Description
Claims
Application Information

- R&D
- Intellectual Property
- Life Sciences
- Materials
- Tech Scout
- Unparalleled Data Quality
- Higher Quality Content
- 60% Fewer Hallucinations
Browse by: Latest US Patents, China's latest patents, Technical Efficacy Thesaurus, Application Domain, Technology Topic, Popular Technical Reports.
© 2025 PatSnap. All rights reserved.Legal|Privacy policy|Modern Slavery Act Transparency Statement|Sitemap|About US| Contact US: help@patsnap.com