Automobile fender side flanging, side shaping and side punching composite die
A technology for automobile fenders and composite molds, which is applied in the field of composite molds for side turning, side shaping, and side punching of automobile fenders. It can solve the problems of lower production efficiency, compound stamping process, and heavy quality, and reduce the number of processing strokes. Cost, reduced floor space, development cost saving effect
- Summary
- Abstract
- Description
- Claims
- Application Information
AI Technical Summary
Problems solved by technology
Method used
Image
Examples
Embodiment Construction
[0051] The present invention will be further described below in conjunction with the accompanying drawings and specific embodiments.
[0052] Such as figure 1 Shown is the geometric model of the fender of an SUV model, the material is JAC270D-45 / 45, which is equivalent to Baosteel material DC54D+ZF-45 / 45, the plate thickness is 0.65mm, the yield strength Ys=120-220MPa, and the tensile strength Ts =260~350MPa, work hardening index n≥0.2, thickness anisotropy index r≥1.8, elongation after fracture El≥36%, product outer contour size is 1018mm×780mm×212mm. Automobile fenders are constructed of complex spatial surfaces, with a small surface curvature radius and large curvature fluctuations of adjacent surfaces. Multiple assembly parts such as headlights and hoods have an assembly relationship.
[0053] The fender OP10 is a drawing sequence. In order to ensure that the fender is fully formed and avoid cracking, wrinkling and surface defects, corresponding process supplementary sur...
PUM
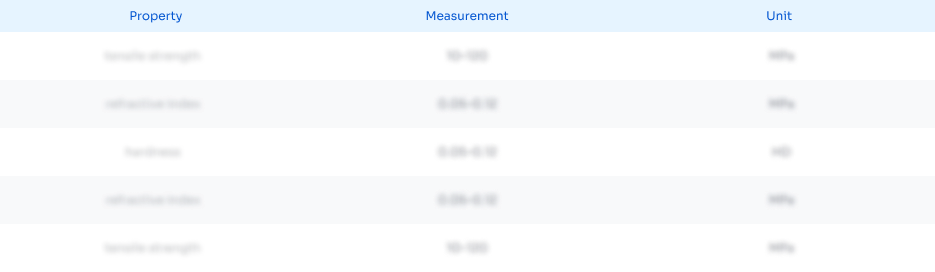
Abstract
Description
Claims
Application Information

- R&D Engineer
- R&D Manager
- IP Professional
- Industry Leading Data Capabilities
- Powerful AI technology
- Patent DNA Extraction
Browse by: Latest US Patents, China's latest patents, Technical Efficacy Thesaurus, Application Domain, Technology Topic, Popular Technical Reports.
© 2024 PatSnap. All rights reserved.Legal|Privacy policy|Modern Slavery Act Transparency Statement|Sitemap|About US| Contact US: help@patsnap.com