High-temperature flame-retardant foaming agent and preparation method thereof
A foaming agent, high temperature technology, applied in the field of high temperature flame retardant foaming agent and its preparation, can solve the problems of the need to improve foam stability, poor compatibility between organic foaming agent and polymer substrate, etc.
- Summary
- Abstract
- Description
- Claims
- Application Information
AI Technical Summary
Problems solved by technology
Method used
Image
Examples
Embodiment 1
[0036] A high-temperature flame-retardant foaming agent, comprising the following raw materials in parts by weight: 20 parts of azodicarbonamide, 10 parts of gelatin, 0.1 part of alkaline protease, 8 parts of flame-retardant mesoporous silica, and 15 parts of deionized water ;
[0037] The high temperature flame retardant foaming agent is made by the following steps:
[0038] Step A1, add gelatin and alkaline protease to distilled water, add sodium hydroxide solution, adjust the pH to 12, react in a constant temperature water bath environment at a temperature of 50°C for 1 hour, cool to room temperature, add hydrochloric acid solution for neutralization, and then filter , the filter cake was dried at 60°C to constant weight to obtain a protein foaming agent;
[0039] Step A2, add flame-retardant mesoporous silica to deionized water, add azodicarbonamide and ultrasonically disperse at a frequency of 40kHz for 30min, then add the protein-type foaming agent prepared in step A1, ...
Embodiment 2
[0058] A high-temperature flame-retardant foaming agent, comprising the following raw materials in parts by weight: 25 parts of azodicarbonamide, 12 parts of gelatin, 0.2 parts of alkaline protease, 9 parts of flame-retardant mesoporous silica, and 20 parts of deionized water ;
[0059] The high temperature flame retardant foaming agent is made by the following steps:
[0060] Step A1, add gelatin and alkaline protease to distilled water, add sodium hydroxide solution, adjust the pH to 12.5, react in a constant temperature water bath environment at a temperature of 52°C for 1.5 hours, cool to room temperature, add hydrochloric acid solution for neutralization, and then filter , the filter cake was dried at 63°C to constant weight to obtain a protein foaming agent;
[0061] Step A2, add flame-retardant mesoporous silica to deionized water, add azodicarbonamide and ultrasonically disperse at a frequency of 50kHz for 40min, then add the protein-type foaming agent prepared in ste...
Embodiment 3
[0080] A high-temperature flame-retardant foaming agent, comprising the following raw materials in parts by weight: 30 parts of azodicarbonamide, 15 parts of gelatin, 0.3 parts of alkaline protease, 10 parts of flame-retardant mesoporous silica, and 25 parts of deionized water ;
[0081] The high temperature flame retardant foaming agent is made by the following steps:
[0082] Step A1, add gelatin and alkaline protease to distilled water, add sodium hydroxide solution, adjust the pH to 13, react in a constant temperature water bath environment at a temperature of 55°C for 2 hours, cool to room temperature, add hydrochloric acid solution for neutralization, and then filter , the filter cake was dried at 65°C to constant weight to obtain a protein foaming agent;
[0083] Step A2, add flame-retardant mesoporous silica to deionized water, add azodicarbonamide and ultrasonically disperse at a frequency of 60kHz for 60min, then add the protein foaming agent prepared in step A1, at...
PUM
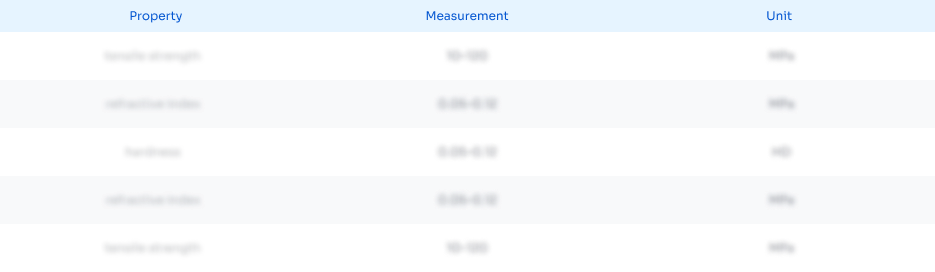
Abstract
Description
Claims
Application Information

- R&D
- Intellectual Property
- Life Sciences
- Materials
- Tech Scout
- Unparalleled Data Quality
- Higher Quality Content
- 60% Fewer Hallucinations
Browse by: Latest US Patents, China's latest patents, Technical Efficacy Thesaurus, Application Domain, Technology Topic, Popular Technical Reports.
© 2025 PatSnap. All rights reserved.Legal|Privacy policy|Modern Slavery Act Transparency Statement|Sitemap|About US| Contact US: help@patsnap.com