Remote-control thermal-state wet-process injection lining making method
A wet method and injection molding technology, applied in furnaces, furnace types, blast furnace parts, etc., can solve problems such as difficulty in uniformity, and achieve the effects of low rebound rate, improved operating environment, and improved strength and wear resistance.
- Summary
- Abstract
- Description
- Claims
- Application Information
AI Technical Summary
Problems solved by technology
Method used
Image
Examples
Embodiment Construction
[0023] A method for remote-controlled thermal wet injection lining, comprising the following steps:
[0024] S1. Equipment admission: install and debug the equipment one day in advance, and set up two hoisting holes on the furnace wall of blast furnace 3. The hoisting holes are at least 80mm*300mm. The connection line with the manhole on the opposite side is perpendicular to the connection line of the two hoisting holes, and the electric hoist 2 is hoisted in the four holes, and the spraying manipulator 1 is sent into the inside of the blast furnace 3 through the maintenance square hole of the distribution chute on the furnace top, and the spraying manipulator 1 It is connected with four electric hoists 2 so that it is on the central axis of the blast furnace 3, and the spraying manipulator 1 communicates with the injection workstation located outside the blast furnace 3 through a material pipe;
[0025] S2. Fire pressing: lower the material surface in the blast furnace 3 to t...
PUM
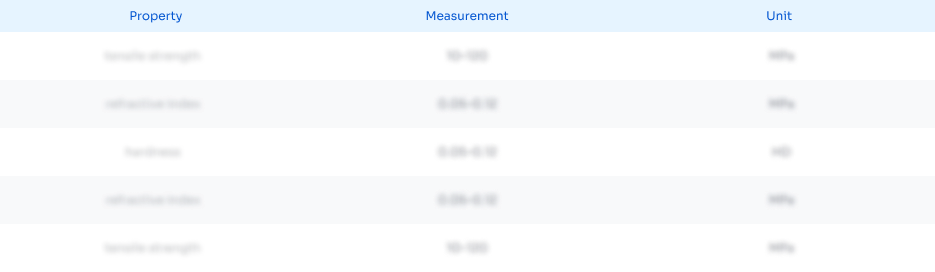
Abstract
Description
Claims
Application Information

- R&D
- Intellectual Property
- Life Sciences
- Materials
- Tech Scout
- Unparalleled Data Quality
- Higher Quality Content
- 60% Fewer Hallucinations
Browse by: Latest US Patents, China's latest patents, Technical Efficacy Thesaurus, Application Domain, Technology Topic, Popular Technical Reports.
© 2025 PatSnap. All rights reserved.Legal|Privacy policy|Modern Slavery Act Transparency Statement|Sitemap|About US| Contact US: help@patsnap.com