Preparation method of denitration catalyst cooperating with NH3 and CO
A technology of denitration catalyst and pore-forming agent, which is applied in the field of preparation of denitration catalyst, can solve the problems of difficulty in meeting flue gas emission standards, increased denitration cost, poor denitration efficiency, etc., achieve excellent low-temperature catalytic denitration activity, and improve CO selectivity. Oxidizing ability, the effect of reducing the amount of injection
- Summary
- Abstract
- Description
- Claims
- Application Information
AI Technical Summary
Problems solved by technology
Method used
Image
Examples
Embodiment 1
[0029] A synergistic NH 3 A method for preparing a denitration catalyst with CO, comprising the steps of:
[0030] 1) Dissolve 10g of manganese nitrate, 13g of cerium nitrate, 35g of cobalt nitrate, 3g of propylene glycol and 2g of field green powder in deionized water, heat to 40-45°C, and stir thoroughly;
[0031] 2) Add 0.125mol / L Na 2 CO 3 Add dropwise to the solution in step 1), keep the pH value of the solution at 7.5-9, and stir continuously for 2.5-3 hours to promote the precipitation of metal salts;
[0032] 3) Filter the precipitate obtained in step 2), and wash with distilled water (40-60°C), repeat 3-5 times to completely remove impurities;
[0033] 4) The solid obtained in step 3) was dried at 50°C for 48 hours, and calcined at 500°C for 3 hours, and the heating rate was set at 2-15°C / min to obtain the desired catalyst.
Embodiment 2
[0035] A synergistic NH 3 A method for preparing a denitration catalyst with CO, comprising the steps of:
[0036] 1) Dissolve 10g manganese acetate, 3g cerium nitrate, 27g cobalt chloride, 1.5g copper nitrate, 2g propylene glycol and 1.5g PVP in deionized water, heat to 40-45°C, and stir thoroughly;
[0037] 2) Add 0.150mol / L Na 2 CO 3 Add dropwise to the solution in step 1), keep the pH value of the solution at 7.5-8.5, and stir continuously for 3-4 hours to promote the precipitation of metal salts;
[0038] 3) Filter the precipitate obtained in step 2), and wash with distilled water (40-45°C), repeat 3-5 times, and completely remove impurities;
[0039] 4) The solid obtained in step 3) was dried at 70°C for 36 hours, and calcined at 450°C for 3.5 hours, and the heating rate was set at 5-10°C / min to obtain the desired catalyst.
Embodiment 3
[0041] A synergistic NH 3 A method for preparing a denitration catalyst with CO, comprising the steps of:
[0042] 1) Dissolve 8g of manganese acetate, 32g of cobalt chloride, 2.5g of copper nitrate, 1.5g of propylene glycol and 2g of PEG in deionized water, heat to 50-60°C, and stir thoroughly;
[0043] 2) Add 0.3mol / L ammonia water dropwise to the solution in step 1), keep the pH value of the solution at 8.0-8.5, and stir continuously for 2-3 hours to promote the precipitation of metal salts;
[0044] 3) Filter the precipitate obtained in step 2), and wash with distilled water (40-45°C), repeat 3-5 times, and completely remove impurities;
[0045] 4) The solid obtained in step 3) was dried at 80°C for 28 hours, and calcined at 500°C for 3 hours, and the heating rate was set at 2-10°C / min to obtain the desired catalyst.
[0046] Under the condition of simulated flue gas, the performance of the denitrification catalyst was evaluated, and the NH 3 As a reducing agent, the re...
PUM
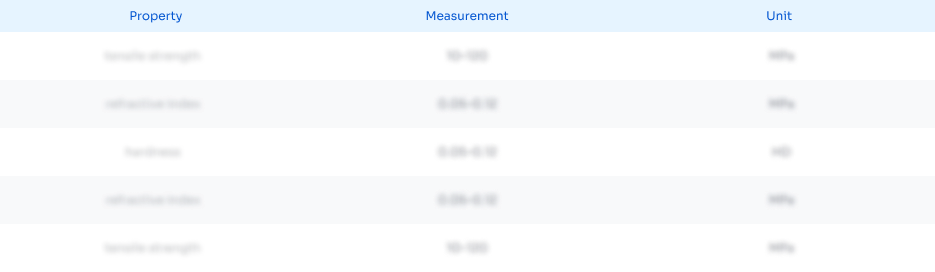
Abstract
Description
Claims
Application Information

- Generate Ideas
- Intellectual Property
- Life Sciences
- Materials
- Tech Scout
- Unparalleled Data Quality
- Higher Quality Content
- 60% Fewer Hallucinations
Browse by: Latest US Patents, China's latest patents, Technical Efficacy Thesaurus, Application Domain, Technology Topic, Popular Technical Reports.
© 2025 PatSnap. All rights reserved.Legal|Privacy policy|Modern Slavery Act Transparency Statement|Sitemap|About US| Contact US: help@patsnap.com