Preparation method of multilayer foamed nickel composite material capable of being used for water-in-oil emulsion separation
A water-in-oil emulsion and composite material technology, which is applied in the field of three-dimensional water-in-oil emulsion separation membrane preparation, can solve membrane fouling and other problems, and achieve easy preparation process, excellent chemical stability and mechanical stability, and high separation efficiency Effect
- Summary
- Abstract
- Description
- Claims
- Application Information
AI Technical Summary
Problems solved by technology
Method used
Image
Examples
Embodiment 1
[0032] (1). Preliminary preparation for the experiment:
[0033] The nickel foam was cut to a size of 3×3cm and ultrasonically cleaned in ethanol for 30 minutes, then washed with deionized water and dried in an oven for later use.
[0034] (2). Suspension preparation:
[0035] Add 0.1 g of carbon nanoparticles (CNPs), 1 g of polydimethylsiloxane (PDMS) and 0.1 g of curing agent (184 silicone rubber) into 50 g of n-hexane, and use a frequency of 30 KHz for 1 h to form a stable Suspended and stored for later use.
[0036] (3). Preparation of single-layer nickel foam composite material:
[0037] Immerse the foamed nickel flakes cleaned and dried in the step in the suspension, and place at room temperature until the solvent evaporates, and the mixture of carbon nanoparticles (CNPs) and polydimethylsiloxane (PDMS) is uniformly deposited on the interior and surface of the foamed nickel . Then place it in a muffle furnace at 100° C. for 1 hour to make it solidify, and then a sing...
Embodiment 2
[0043] (1). Preliminary preparation for the experiment:
[0044] The nickel foam was cut to a size of 3×3cm and ultrasonically cleaned in ethanol for 30 minutes, then washed with deionized water and dried in an oven for later use.
[0045] (2). Suspension preparation:
[0046]Add 0.1 g of carbon nanoparticles (CNPs), 1 g of polydimethylsiloxane (PDMS) and 0.1 g of curing agent (184 silicone rubber) into 50 g of n-hexane, and use a frequency of 30 KHz for 1 h to form a stable Suspended and stored for later use.
[0047] (3). Preparation of single-layer nickel foam composite material:
[0048] Immerse the foamed nickel flakes cleaned and dried in the step in the suspension, and place at room temperature until the solvent evaporates, and the mixture of carbon nanoparticles (CNPs) and polydimethylsiloxane (PDMS) is uniformly deposited on the interior and surface of the foamed nickel . Then place it in a muffle furnace at 100° C. for 1 hour to make it solidify, and then a singl...
Embodiment 3
[0054] (1). Preliminary preparation for the experiment:
[0055] The nickel foam was cut to a size of 3×3cm and ultrasonically cleaned in ethanol for 30 minutes, then washed with deionized water and dried in an oven for later use.
[0056] (2). Suspension preparation:
[0057] Add 0.1 g of carbon nanoparticles (CNPs), 1 g of polydimethylsiloxane (PDMS) and 0.1 g of curing agent (184 silicone rubber) into 50 g of n-hexane, and use a frequency of 30 KHz for 1 h to form a stable Suspended and stored for later use.
[0058] (3). Preparation of single-layer nickel foam composite material:
[0059] Immerse the foamed nickel flakes cleaned and dried in the step in the suspension, and place at room temperature until the solvent evaporates, and the mixture of carbon nanoparticles (CNPs) and polydimethylsiloxane (PDMS) is uniformly deposited on the interior and surface of the foamed nickel . Then place it in a muffle furnace at 100° C. for 1 hour to make it solidify, and then a sing...
PUM
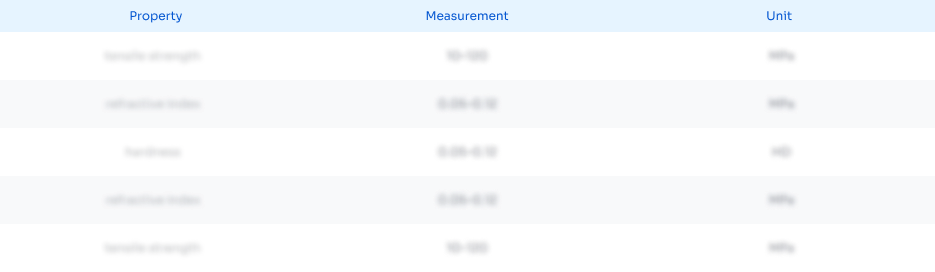
Abstract
Description
Claims
Application Information

- Generate Ideas
- Intellectual Property
- Life Sciences
- Materials
- Tech Scout
- Unparalleled Data Quality
- Higher Quality Content
- 60% Fewer Hallucinations
Browse by: Latest US Patents, China's latest patents, Technical Efficacy Thesaurus, Application Domain, Technology Topic, Popular Technical Reports.
© 2025 PatSnap. All rights reserved.Legal|Privacy policy|Modern Slavery Act Transparency Statement|Sitemap|About US| Contact US: help@patsnap.com